Compression tubing couplers are essential components in a variety of industries, serving as critical connectors that ensure seamless fluid or gas flow within piping systems. Understanding their unique features, applications, and the engineering behind them can significantly enhance operational efficiency. This article explores the multifaceted nature of compression tubing couplers, backed by solid expertise and authoritative insights.
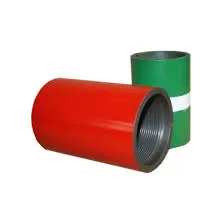
Compression tubing couplers are designed to join two sections of tubing, providing a leak-proof seal without the need for welding or solvent-gluing, which could otherwise compromise structural integrity. These couplers are vital in scenarios where frequent assembly or disassembly of piping systems is necessary, providing flexibility and ease of maintenance. The utilization of high-quality materials, such as stainless steel, brass, or plastic composites, ensures that they meet specific industrial requirements, including resistance to corrosion, high pressure, and varying temperature ranges.
Expertise in the selection and application of compression tubing couplers starts with understanding your specific requirements. For instance, industries involving chemical processing may require couplers that can withstand aggressive chemicals without degrading. Stainless steel couplers are often preferred in such situations due to their superior resistance to chemical corrosion and ability to maintain structural integrity under severe conditions. On the other hand, in environments where weight reduction is paramount, plastic composite couplers offer a viable alternative without compromising on performance or reliability.

The authoritative use of compression tubing couplers is emphasized in the oil and gas sector, where ensuring tight seals under high pressure is non-negotiable. Compliance with industry standards, such as those set by the American Society of Mechanical Engineers (ASME) or the International Organization for Standardization (ISO), is critical. These standards ensure that the products deliver optimum performance and safety. Experienced engineers often rely on comprehensive testing and validation processes to certify that couplers can handle specific operational pressures and stresses before installation.
Trustworthiness in the manufacturing and provision of compression tubing couplers involves rigorous quality control procedures. Leading manufacturers in this domain typically employ advanced manufacturing techniques, including CNC machining and laser cutting, to deliver precision-engineered products. Additionally, the adoption of smart technologies, such as IoT-enabled sensors within couplers, offers real-time data analytics, enhancing the predictive maintenance capabilities and reducing the risk of unexpected downtimes.
compression tubing coupler
Furthermore, the real-world experience of end-users plays a pivotal role in the evolution and refinement of compression tubing coupler designs. Feedback collected from industries ranging from pharmaceuticals to automotive manufacturing provides practical insights into performance under various operational conditions. Manufacturers are increasingly engaging in collaborative relationships with their clients to tailor solutions that address specific challenges, thereby fostering a cycle of continuous improvement.
The advancements in material science also pave the way for future innovations in compression tubing coupler technology. Nanotechnology, for instance, is opening new avenues for creating materials with customized properties, such as enhanced durability, thermal stability, and self-healing surfaces. These innovations not only extend the lifespan of couplers but also contribute to sustainable practices by reducing waste and the frequency of replacements.
Understanding the mechanics of compression tubing couplers is equally crucial for ensuring their proper installation and maintenance. Operators must be adept at interpreting pressure ratings, understanding the compatibility of mating surfaces, and selecting appropriate types of seals—be it elastomeric or metallic—to suit their application scenarios. Regular training sessions and access to detailed technical manuals greatly enhance operational expertise, leading to prolonged service life and reduced operational costs.
Investing in quality compression tubing couplers, backed by evidence-based engineering and user-centric design improvements, plays a substantial role in optimizing the performance of fluid and gas systems across various industries. Their influence on system integrity, efficiency, and safety accentuates their importance as indispensable components in modern industrial applications. Following best practices in selection, installation, and ongoing maintenance will provide invaluable benefits, including enhanced reliability, safety, and profitability of operations.