The world of engineering often shines a spotlight on the ingenuity embedded in coupling blanks. These components, although seemingly modest in nature, serve as essential connectors in mechanical and industrial assemblies, providing the riveting backbone of many complex systems. Through personal experiences in the field of machine design, numerous insights highlight the significance of coupling blanks that extend far beyond their basic function.
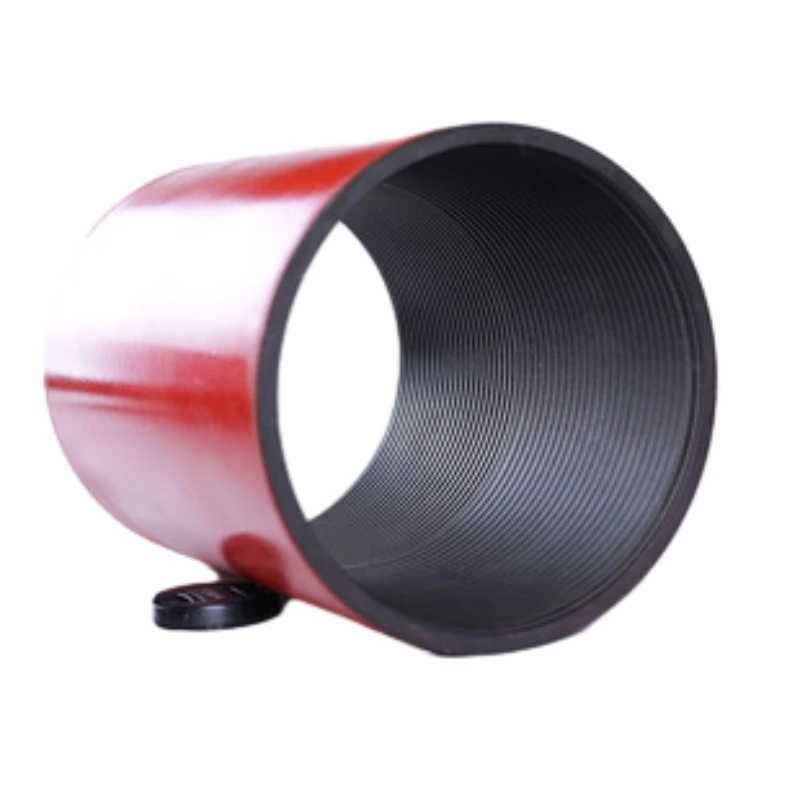
Picture entering a factory where the hum of machinery is a constant, reassuring buzz. Here, coupling blanks find their stage, seamlessly interlocking various machine parts and ensuring their synchronized operation. Years of hands-on experience reveal that selecting the right coupling blank can make or break a project. An engineer's selection process is akin to a craftsman's meticulous choice of materials; it's pivotal for optimal performance and longevity of mechanical assemblies.
The selection of coupling blanks demands both expertise and precision. They must be shaped from materials that suit the operating environment—stainless steel for corrosion resistance, or aluminum for lightweight applications are common choices among professionals. The mechanical properties, such as torsional rigidity and flexibility, must align with the specific design requirements. Engineers with a profound understanding of material science and mechanical engineering are best equipped to make these determinations, thus ensuring operational efficiency and durability.
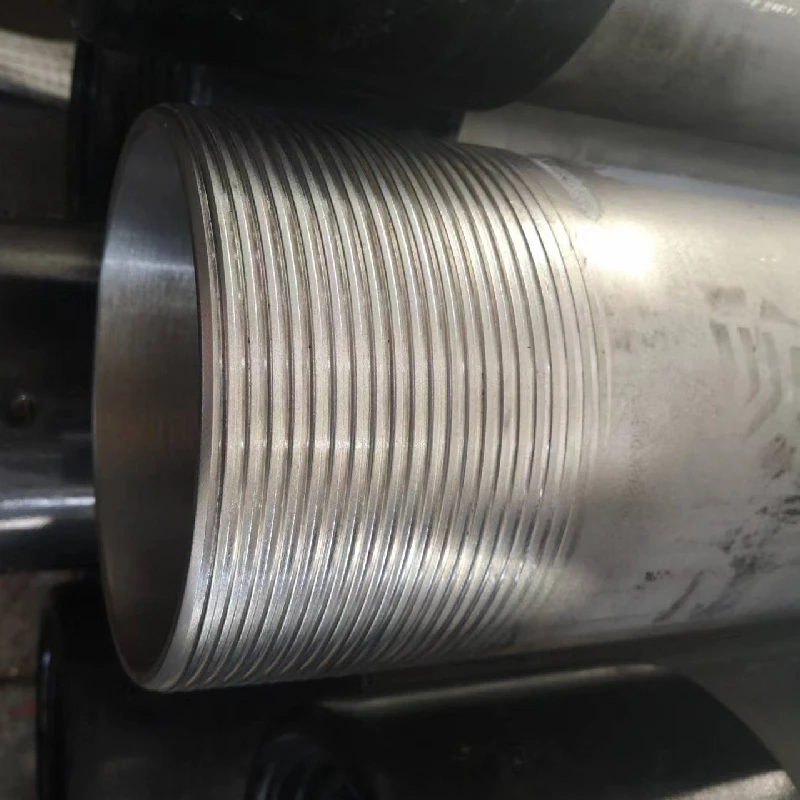
In addition to material selection, the design intricacies of coupling blanks require authoritative scrutiny. Experienced engineers often discuss the often-overlooked influence of coupling geometry on performance. For instance, a serpentine design might offer greater flexibility, while a compact, solid form could provide enhanced strength. Balancing these attributes demands a keen understanding of mechanical principles, cultivated through years of practical application.
coupling blank
Trustworthiness in the realm of coupling blanks extends to manufacturing precision. The production process—a blend of skillful machining and rigorous quality assurance—dictates reliability. Companies with a reputation for producing high-quality coupling blanks often leverage cutting-edge CNC technology, ensuring precision down to the micron. Through stringent ISO-certified processes, these manufacturers build trust, guaranteeing each coupling blank meets demanding industrial standards.
An often-discussed, yet crucial factor in the realm of coupling blanks is their adaptability.
Modern mechanical systems are evolving constantly. Thus, coupling blanks must offer versatility, able to be used across a range of applications from automotive drives to industrial conveyor systems. This demands a forward-thinking approach in both engineering practices and manufacturing techniques to anticipate and meet future challenges.
Ultimately, the journey of every coupling blank—from a raw piece of metal to a finished product integral to machinery—is a testament to the symbiotic relationship between skilled professionals and trusted manufacturers. Through the synergy of experience, expertise, authority, and trust, these often-overlooked components ensure the world of machinery remains steadfast and reliable.
As the global demand for efficient and sustainable mechanical solutions continues to grow, coupling blanks stand as a symbol of innovation and reliability. Their understated simplicity in function belies the complex engineering and expert craftsmanship that goes into each piece. This dedication to excellence, shared by engineers and manufacturers alike, ensures that coupling blanks will remain invaluable in the ever-evolving landscape of industrial technology.