Discovering the ideal coupling for tubing requires more than just standard specifications; it demands a nuanced understanding of material compatibility, pressure ratings, and application environments. Navigating this complex landscape not only requires technical expertise but also relies on hands-on experience to ensure reliability and efficiency.
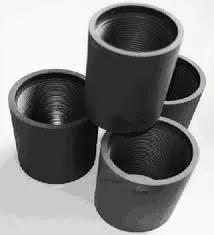
Selecting the right coupling involves an in-depth exploration of the material compatibility with the tubing and the conveyed fluid. Material science plays a pivotal role here. For instance, stainless steel couplings are preferred in environments prone to corrosion, while brass couplings excel in high-pressure scenarios needing reliable sealing. Understanding these distinctions is crucial to optimize performance and longevity, preventing breakdowns and costly repairs.
Pressure ratings and temperature ranges are two other critical parameters in the selection process.
A coupling must be able to withstand the maximum operating pressure to avoid failures. Real-world scenarios often test these limits, making it essential for industries to validate couplings not just through manufacturer specifications but also via rigorous field testing. Couplings such as those designed for hydraulic systems will demand different specifications than those used in pneumatic systems. Each application presents unique demands and challenges that necessitate appropriate solutions.

Application environment consideration extends beyond immediate use conditions to anticipated future changes, such as variations in temperature and pressure. End users with extensive installation experience often highlight the importance of foresight in predictive maintenance and life cycle costing. These expert insights prove invaluable in environments like the oil and gas industry, where extremes of temperature and pressure are prevalent.
coupling for tubing
Manufacturers and suppliers of tubing couplings constantly innovate to align with Industry 4.0 standards. Smart couplings with integrated sensors could be the future, offering real-time data on pressure and temperature to predict potential failures before they occur. Leveraging IoT technology, these advancements promise to transform predictive maintenance into a more exact science, reducing downtimes and enhancing the reliability of tubing systems.
Moreover, industry standards and compliance play a critical role in ensuring the trustworthiness of couplings. Standards set by organizations like ASTM or ISO are not just bureaucratic formalities but rigorous benchmarks ensuring safety and quality. Manufacturers who adhere to these standards offer a significant reassurance to their clients, underscoring their commitment to producing high-quality and reliable components.
In conclusion, selecting the right coupling for tubing is a dynamic process that balances technical specifications with real-world applications. It is a harmonious blend of material science, engineering expertise, and field experience. This holistic approach, augmented by future-facing innovations and stringent compliance with industry standards, empowers the selection of couplings that not only meet but exceed expectations, ensuring operational safety and efficiency. This strategy ultimately instills confidence and builds enduring relationships between manufacturers, suppliers, and end-users, creating a cycle of trust and reliability that defines success in the industry.