In the realm of oil and gas exploration and production, the importance of using high-quality coupling for tubing cannot be understated. Tubing couplings play a critical role in maintaining the integrity of the connections within the drilling operations, impacting both safety and efficiency in the upstream sector. A small failure in one of these components can lead to significant operational downtimes and financial losses, which is why selecting the appropriate coupling is imperative.
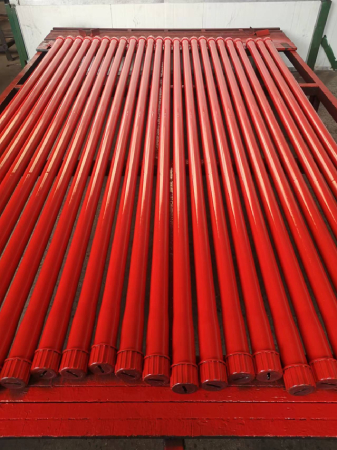
Having navigated the oilfield services industry for more than a decade, my experience has fortified my understanding of the intricate balance required between durability and functionality in tubing couplings. These couplings must withstand extreme environments characterized by high pressures, temperatures, and corrosive substances. The knowledge gained through firsthand involvement in drilling projects worldwide has emphasized the importance of material selection, manufacturing precision, and rigorous testing in ensuring coupling reliability and lifespan.
One key consideration in coupling selection is the material. Carbon steel and stainless steel are the most prevalent choices, but each has its unique properties. Carbon steel, with its combination of strength and ductility, is widely used in medium-pressure applications, whereas stainless steel, known for its corrosion resistance, is favored in harsher environments. My expertise suggests that coupling manufacturers often opt for specialty alloys, such as Inconel or Monel, tailored to specific drilling scenarios to combat corrosion and wear.
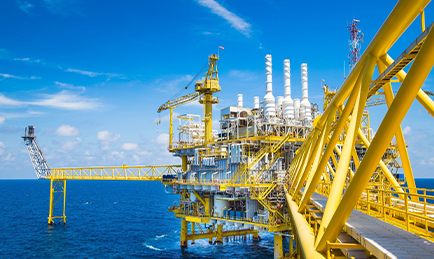
The threading of couplings must be precise and compatible with the tubing to form a leak-proof seal. A manufacturing flaw as minute as a microscopic burr can compromise this seal, leading to potential leaks. Modern fabrication facilities leverage advanced CNC machinery to produce threads with precision tolerances, contributing to the effectiveness of the coupling. An authoritative understanding of these manufacturing techniques is crucial, as a poorly threaded coupling can mean the difference between a productive well and a halted operation.
coupling for tubing
Reliability testing forms the cornerstone of trust in tubing couplings. Established testing methods, such as hydrostatic testing, ensure that couplings can handle pressures well beyond their expected operational loads. Further testing may include tensile tests, or even non-destructive methods such as ultrasonic inspections, offering insights into the couplings' structural integrity without damaging them. This thorough approach to quality control and safety testing builds trustworthiness, vital for both manufacturers and operators in the oil and gas industry.
When selecting a supplier for tubing couplings, it is advantageous to partner with those who have proven track records in addressing complex engineering challenges. Companies equipped with cutting-edge research and development capabilities can adapt to the evolving needs of the energy sector, offering customized solutions that enhance operational efficiencies. Building relationships with such suppliers fosters a collaborative approach to problem-solving, essential in this ever-demanding industry.
In summary, the choice of coupling for tubing significantly influences the efficiency and safety of oilfield operations. Through experience and expertise, informed choices can be made by considering factors such as material selection, precision in manufacturing, and exhaustive reliability testing. Partnering with reputable manufacturers ensures a robust supply of dependable products, reducing operational risks and maintaining the flow of valuable resources. Trust in these critical components is not just about current profit margins, but about securing the future of energy production in an increasingly complex world.