In the vast realm of industrial applications, choosing the right coupling for tubing is paramount for maintaining system efficiency and safety. A coupling serves as the crucial connector between lengths of tubing, ensuring fluid flow or the containment of gasses in a controlled manner. Thus, understanding the nuances of selecting the right coupling for tubing is not only instrumental for the performance but equally critical in preventing potential operational failures.
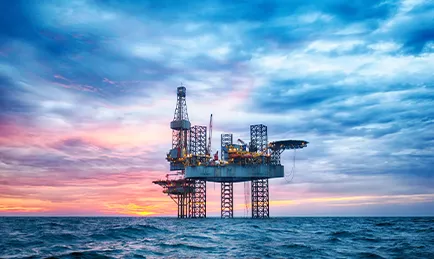
Experience teaches us that material compatibility is the foremost consideration. Tubing is fabricated from a myriad of materials—ranging from metals like stainless steel, copper, or brass, to plastics such as PVC and polyethylene. Ensuring the coupling material does not react adversely with the tubing material is essential for longevity and reliability. For instance, a stainless-steel coupling is an optimal choice for stainless steel tubing, primarily because of its superior resistance to corrosion and temperature fluctuations.
The second component in selecting an optimal coupling is to evaluate the application-specific requirements, including pressure ratings, environmental exposures, and types of fluids involved. High-pressure systems necessitate robust couplings, typically made from high-strength metals or advanced polymers. Expertise in the domain reveals that neglecting this aspect can lead to system failures that not only cause downtime but may also incur significant safety hazards.
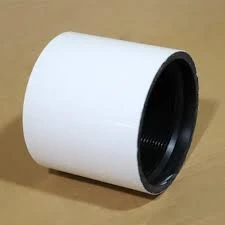
The coupling design is integral in the selection process. Push-to-connect couplings offer the advantage of ease and speed in installations, which is ideal for systems necessitating frequent maintenance or adjustments. Conversely, threaded couplings, while more labor-intensive to install, provide superior mechanical grip and are suited for high-vibration or high-pressure environments. Guidance from authoritative sources recommends flange couplings as a solution when easy disassembly of tubing is required, such as in cleaning or inspection scenarios.
coupling for tubing
From a credibility standpoint, regulatory and compliance standards cannot be overlooked. Industry standards such as those defined by ASTM, ANSI, or ISO ensure that couplings meet specific performance and safety criteria. Certifications from these bodies enhance the trustworthiness of the couplings, a crucial factor in sectors like pharmaceuticals or food processing, where regulatory compliance is non-negotiable.
Furthermore, in high-purity or sanitary environments, the choice of coupling takes precedence with additional factors like sterilizability and resistance to microbial growth. Tri-clamp couplings, for example, are extensively employed in such applications due to their quick disconnect design and ability to achieve a secure, leak-proof seal without tools, minimizing contamination risks.
Investing in high-quality couplings from reputable manufacturers can drastically extend the lifecycle of your tubing systems, an insight gained from experience across industries. While upfront costs may be higher, the return on investment is realized through reduced maintenance costs and avoidance of system failures.
In sum, selecting the correct coupling for tubing is a multi-faceted decision that hinges on understanding the full spectrum of application demands and aligning them with the coupling's design and material properties. This vigilant approach not only enhances operational efficiency but solidifies your system's reliability—a standing testament to both expertise and authority in the realm of industrial tubing applications.