Selecting the right coupling for tubing can significantly enhance the performance and reliability of your fluid transfer systems. While often overlooked, this small component plays a pivotal role across various industries, including oil and gas, pharmaceuticals, and food processing. A sophisticated understanding of coupling for tubing is essential for maximizing system efficiency and ensuring robust operation.
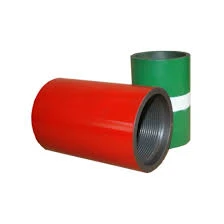
First and foremost, expertise in the subject dictates focusing on material compatibility and chemical resistance. Couplings are available in a range of materials such as stainless steel, brass, polyethylene, and more. Each material type caters to different applications. For instance, stainless steel couplings boast superior durability and are suited for high-pressure and high-temperature environments often found in oil & gas industries. Conversely, polyethylene couplings are more appropriate for cost-sensitive projects dealing with non-corrosive fluids. It's crucial to evaluate the chemical properties of the substances being transported to prevent any detrimental reactions that may compromise the coupling's integrity.
Another aspect underlining the expertise in tubing coupling is the connection type. Selecting the appropriate connection type can significantly affect installation time and maintenance costs. The most common connection types include threaded, compression, and quick-connect couplings. Threaded couplings provide a secure connection but may require more time to install. Compression fittings offer a balance of ease and security, often used in water and gas lines. Quick-connect couplings provide convenience and speed, ideal for applications requiring frequent disconnection and reconnection, such as equipment testing facilities.
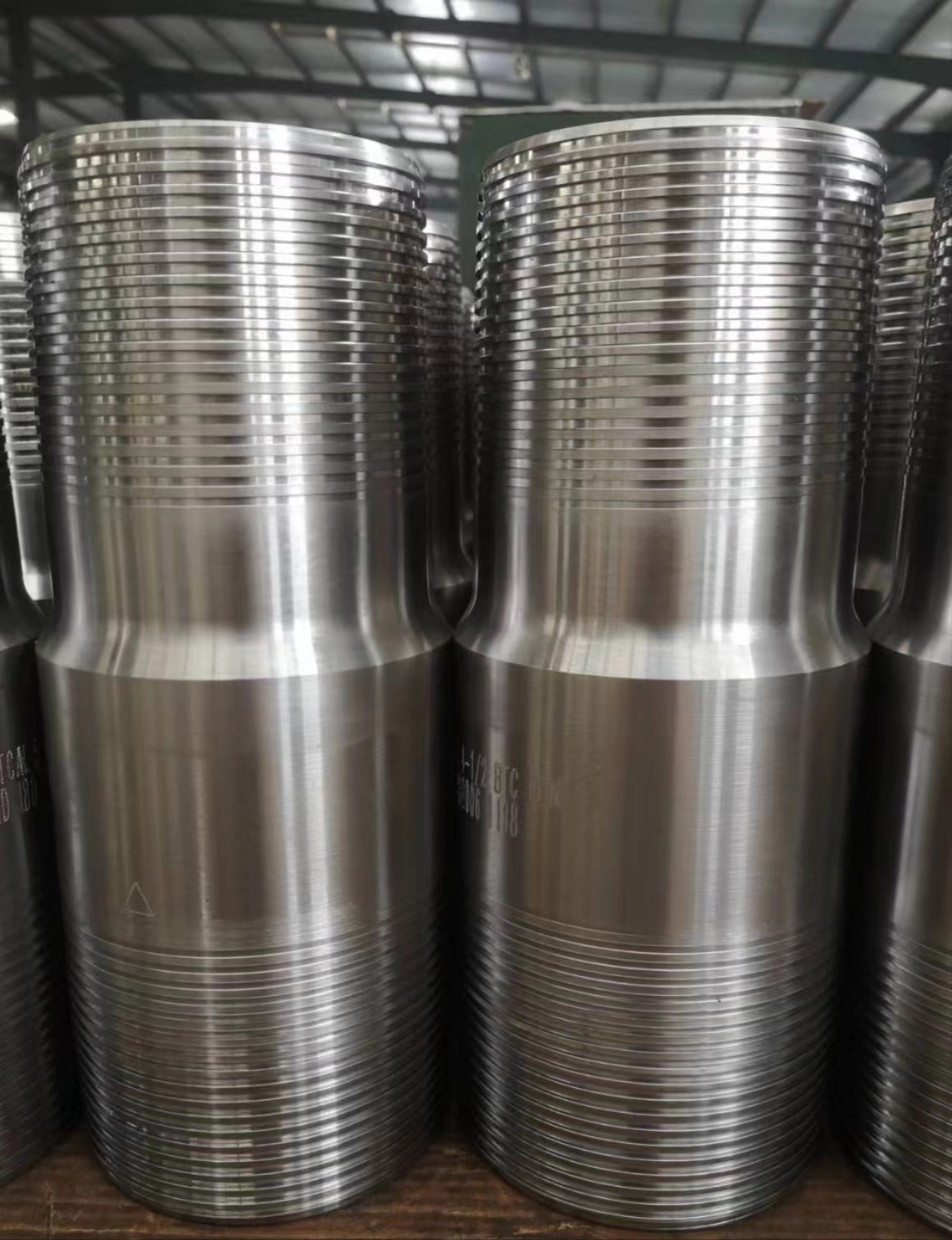
From an experiential viewpoint, understanding the specific application demands is vital. For example, in large-scale pharmaceutical production, where sterile conditions are paramount, cleanroom-grade couplings that prevent contamination are essential. Additionally, considering factors such as temperature fluctuations, pressure changes, and vibration can hugely impact the choice of coupling type and material, ensuring that the coupling performs flawlessly under varied operational conditions.
coupling for tubing
The authoritativeness in selecting the right coupling for tubing also involves aligning with industry standards and certifications. Recognized standards such as ISO, ANSI, and DIN guarantee that the coupling meets rigorous quality and safety requirements. Compliance with these standards is a testament to the coupling’s reliability and performance, instilling trust in its suitability for critical operations.
Furthermore, the reputable manufacturers of tubing couplings often offer insightful resources and support. Choosing a coupling from a manufacturer with comprehensive technical support and a solid warranty reflects their confidence in the product's quality. Engaging with manufacturers also provides guidance on installation and maintenance best practices, reducing the risk of system failures and extending the coupling’s lifecycle.
Trustworthiness of information is key when deciding on the right coupling for your tubing. Collecting data from case studies, customer testimonials, and peer-reviewed technical papers can offer invaluable insights. Insights derived from real-world applications reinforce the practicality and reliability of specific couplings, giving you confidence in your choice.
In conclusion, the quest for the perfect coupling extends beyond just finding a component that 'fits'. It demands a blend of material expertise, connection type knowledge, application-specific considerations, adherence to industry standards, and reputable sourcing. Adopting this multifaceted approach ensures that the chosen coupling not only enhances the system’s performance but also stands as a pillar of reliability and security in a demanding industrial landscape.