In the intricate realm of fluid and gas transfer systems, coupling tube fittings emerge as a quintessential component, embodying the very essence of precision engineering. These small yet mighty instruments play a pivotal role in ensuring the seamless flow and secure connection of various tubular structures within diverse industrial settings. This article delves into the unparalleled significance of coupling tube fittings, accentuating their function and the technological advancements that have revolutionized their application.
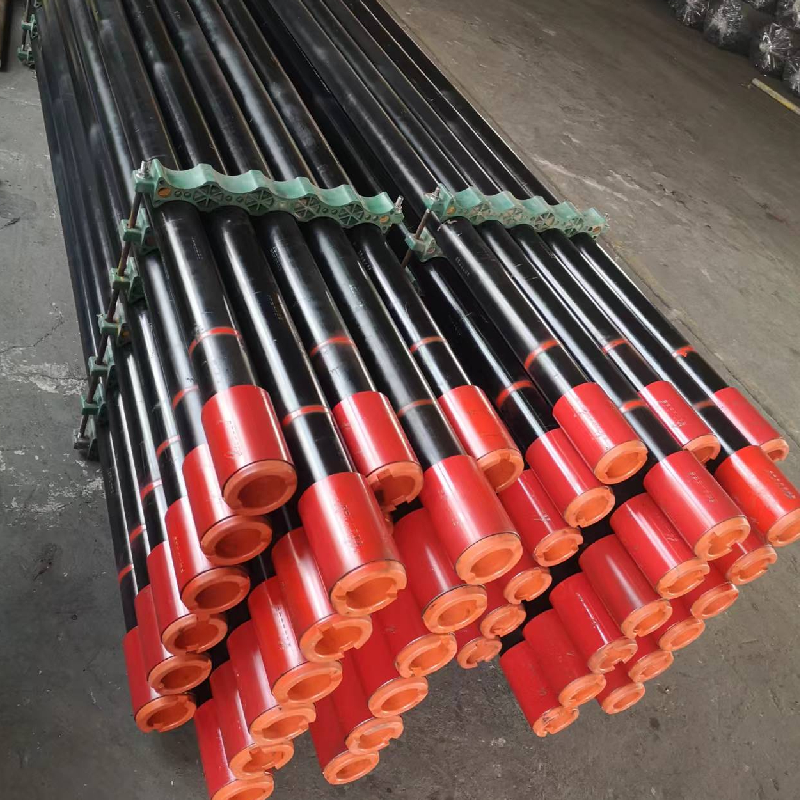
Coupling tube fittings are designed to facilitate the connection and disconnection in piping systems without causing interruptions or leakages. For industries such as petrochemical, pharmaceutical, and aerospace, where precision and reliability are paramount, these fittings serve as the linchpin that upholds the integrity of the entire operation. They are meticulously engineered to withstand high pressures, extreme temperatures, and corrosive environments, ensuring that the transfer process remains unhindered and efficient.
The real-world experience of implementing coupling tube fittings demonstrates their indispensability. A case study from an oil refinery illustrates this point vividly. Faced with the challenge of transporting volatile liquids across complex pipelines, the refinery adopted advanced coupling tube fittings with quick-connect technology. The outcome was noteworthy—a drastic reduction in maintenance shutdowns and a notable increase in operational efficiency. By enabling rapid assembly and disassembly, these fittings alleviated operational bottlenecks and facilitated smooth transitions, underscoring their capability to enhance productivity.
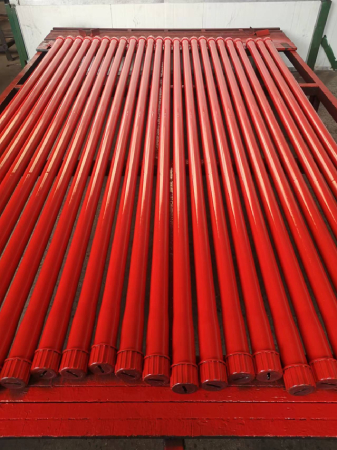
From a professional expertise perspective, coupling tube fittings are crafted from a range of materials, including stainless steel, brass, and various polymers, each catering to specific industry requirements. The choice of material is crucial as it directly impacts the fitting's durability and compatibility with the conveyed media. Stainless steel, renowned for its robustness and resistance to corrosion, is extensively used in chemical processing industries. Conversely, for applications involving pneumatic systems, lightweight polymer fittings are preferred for their ease of installation and effectiveness in high-frequency operations.
coupling tube fitting
Authoritativeness in the design and application of coupling tube fittings is demonstrated by industry certifications and compliance with established standards such as ASME, DIN, and ISO. These standards not only assure quality and performance but also facilitate global interoperability, making it easier for engineers to incorporate these fittings into international projects. Moreover, the continuous evolution of these standards reflects the ongoing innovation in the field, driven by the latest technological advancements and the increasing demand for higher performance and reliability.
Trustworthiness, a critical metric for end-users, is built on the consistent delivery of quality and performance. Manufacturers that employ stringent quality control measures and invest in research and development set themselves apart as leaders in the industry. For instance, the integration of smart technologies in coupling tube fittings, such as sensors that monitor connection integrity and detect leaks, exemplifies the commitment to advancing safety and efficiency. These innovations not only reinforce the user’s trust but also pave the way for predictive maintenance, reducing the likelihood of unforeseen failures and extending the service life of the systems.
In conclusion, coupling tube fittings are an embodiment of engineering excellence, pivotal to the smooth and safe operation of fluid and gas systems across diverse industries. By amalgamating cutting-edge technology with time-tested design principles, they cater to the ever-evolving needs of modern industries. Their reliability and efficiency are not merely a nod to their quality but a testament to the continuous innovation that drives their development. As industries push the boundaries of what is possible, coupling tube fittings will undoubtedly remain at the forefront, ensuring that connection and flow are as seamless and secure as the engineers who rely on them every day envision.