In the realm of fluid and gas transport systems, the coupling tube fitting is a critical component, embodying a fusion of expert engineering and practical application. Known for its versatility and reliability, this fitting serves as a linchpin within various industrial and commercial settings, where it facilitates seamless operations in high-pressure or high-temperature environments. The coupling tube fitting is engineered to ensure optimal flow efficiency, reducing potential leakages or losses through its precise construction.
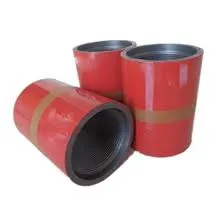
Experience dictates that one of the foremost advantages of coupling tube fittings is their adaptability. Over the years, numerous industries, from petrochemicals to automotive manufacturing,
have utilized these fittings to streamline complex piping systems. Their capability to connect dissimilar materials with minimal risk of expansion or contraction makes them indispensable. In systems where thermal dynamics are crucial, for example, in HVAC units, a coupling tube fitting ensures that fluctuations in temperature do not compromise the integrity of the entire setup.
An exploration into the expertise surrounding coupling tube fittings reveals a meticulous attention to material sciences and mechanical engineering principles. Often fabricated from stainless steel, brass, or other robust alloys, these fittings are designed to withstand environmental stressors such as corrosion, pressure, and vibration. Advanced engineering techniques are employed to ensure each piece meets stringent industry standards, which include rigorous assessments for tensile strength, elasticity, and pressure thresholds. The precision in design, coupled with the integrative use of innovative sealing technologies, enhances their long-standing reputation for dependability.
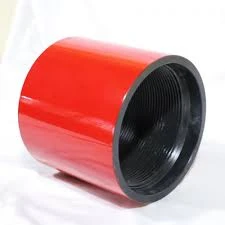
Adding to their authoritativeness, coupling tube fittings are compliant with numerous international and domestic standards, including those outlined by the American Society of Mechanical Engineers (ASME) and the International Standards Organization (ISO). This widespread standardization underscores their suitability for use in critical applications, such as in aerospace technology or industrial chemical processes, where safety and compliance are paramount. Industry professionals often rely on these standards as benchmarks to ensure consistent and safe operational practices.
coupling tube fitting
Trustworthiness in coupling tube fittings is further reinforced by the exhaustive testing procedures that precede their introduction to market. These tests include hydrostatic stress evaluations, vibration endurance trials, and seal integrity assessments—all devised to simulate real-world conditions. Manufacturers of these fittings regularly issue compliance certificates and detailed reports, providing full transparency regarding performance metrics and durability expectations. Such punctual documentation serves as a cornerstone of trust between suppliers and end-users.
Moreover, the installation simplicity and maintenance efficiency associated with coupling tube fittings amplify their appeal. They are designed with user-friendliness in mind, affording engineers and technicians ease of installation without necessitating special tools or advanced skills. This ease of use marks them as both cost-effective and labor-saving solutions, promoting operational fluidity within varying scales of industrial applications.
The productivity gains realized through the use of coupling tube fittings cannot be overstated. Their ability to maintain airtight connections in both standard and aggressive environments directly correlates to reduced downtime and maintenance, thereby fostering enhanced productivity. Industries recognize this ability as not only a mechanical advantage but also a financial one, contributing to the long-term viability and efficiency of their operations.
In summation, the coupling tube fitting is more than just a mechanical component; it is a testament to advanced engineering and industrial innovation. Its role in ensuring the seamless operation of complex systems underscores its integral status within the industrial landscape. From facilitating energy-efficient systems to enabling robust safety standards, the coupling tube fitting exemplifies engineering excellence and remains a pivotal element in both present and future infrastructural endeavors.