Navigating the complex world of oil and gas drilling requires a comprehensive understanding of specialized tools such as drill pipe crossovers. These essential components are the unsung heroes that ensure seamless connectivity between various tools and sections of the drill string. By bridging differences in thread types or sizes, drill pipe crossovers can significantly enhance operational efficiency.

Through years of fieldwork and collaboration with engineers, I’ve come to recognize that selecting the right crossover pipe involves more than just a basic understanding of threading specifications. It demands experience and expertise that can make or break a drilling operation.
Drill pipe crossovers typically connect drill pipes with different thread types, such as API connections or proprietary joints like VAM or Grant Prideco. Understanding the nuances of these connections is crucial. For instance, a mismatch can lead to operational delays or even serious safety hazards. Through empirical evidence gathered from a variety of projects, it is apparent that crossovers with premium threading often yield better torque exposure and provide higher sealing efficiencies.
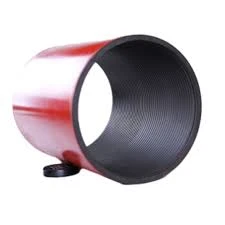
Manufacturers design these tools meticulously to meet specific industry standards, ensuring that they can withstand tremendous operational stress. High-grade materials like AISI 4145H alloy steel are commonly used due to their exceptional strength and durability. This choice of material not only extends the lifespan of the crossover but also ensures compatibility with high-torque operations, which is critical in deeper drilling applications.
For companies aiming to optimize their drilling operations, incorporating high-quality drill pipe crossovers can save significant costs in the long run. When selected correctly, they minimize wear on other drill string components, reducing the frequency of replacements and repairs. This extends the life of the entire drill string, ensuring consistent and efficient drilling performance.
drill pipe crossover
Using the right drill pipe crossover also instills a layer of reliability, essential for meeting tight project deadlines. Having faced the challenge of unexpected downtimes due to faulty or ill-suited equipment, I strongly advocate for rigorous pre-job inspections and thorough understanding of equipment specifications. Proactive maintenance practices, coupled with deploying crossovers tailored to the specific demands of your drill site, can drastically diminish downtime risks.
In terms of trustworthiness, investing in crossovers from reputable suppliers guarantees not just product quality but also expert support. These manufacturers typically provide technical guidance on optimal use and maintenance practices—a critical factor that distinguishes high-quality products from their less reliable counterparts. Ensuring your supplier subscribes to international quality standards should be non-negotiable.
Finally, the relevance of drill pipe crossovers also extends into the digital era.
Leveraging data analytics facilitates the ability to predict crossover wear and tear, optimizing the timing for replacements. Integrating IoT technology within the drill string can provide real-time data analytics, allowing for proactive maintenance and enhancing operational efficacy.
Choosing the right drill pipe crossover is not solely a technical decision but a strategic move that involves leveraging expertise and industry insight. A solid understanding of these components offers a competitive edge in the ever-demanding energy field, where precision, reliability, and efficiency are of paramount importance.