Drill pipe crossovers play an indispensable role in the oil and gas industry, offering critical solutions that ensure seamless operations in various drilling environments. Their primary function is to connect sections of drill pipe that possess different diameters or thread configurations, ensuring compatibility and operational efficiency. This complex, yet essential component calls for an in-depth exploration, reflecting an expert perspective on its production, application, and its pivotal role in industrial operations.
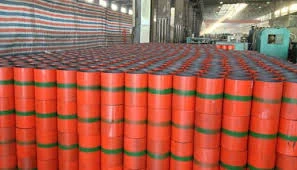
Central to the manufacturing of drill pipe crossovers is the rigorous adherence to industry standards, which guarantees both durability and reliability. These crossovers are typically made from high-strength, heat-treated carbon and alloy steels. Such materials are chosen for their superior mechanical properties, like tensile strength and impact resistance, crucial for withstanding the challenging conditions encountered in drilling operations. The application of precision engineering techniques ensures that these components meet exact dimensional specifications, further contributing to their seamless integration within broader drilling systems.
The expertise required to understand and operate these crossovers cannot be overstated. Drillers rely on them to mitigate issues related to misalignment that could lead to operational inefficiencies or even equipment failure. Experience in selecting the right crossover depends on understanding the different types of threads (such as API connections or proprietary premium threads) and their compatibility with existing equipment. This knowledge is vital for maintaining the integrity and efficiency of the drilling operation, and is a key area where experienced drilling engineers and technicians lend their expertise.
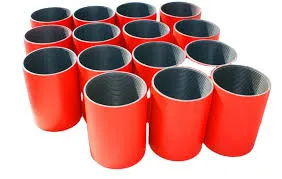
From an authoritative standpoint, the development and application of drill pipe crossovers are guided by recognized industry standards introduced by organizations such as the American Petroleum Institute (API). Compliance with API specifications, such as API Spec 5DP and API Spec 7-1, is non-negotiable, ensuring that products meet stringent quality and safety criteria. Companies investing in advanced research and development continue to innovate, improving upon existing designs to enhance the performance and reliability of crossovers, which is evidenced by testimonies from field operations that highlight reduced downtime and lower operational costs.
drill pipe crossover
Building trust in the use of drill pipe crossovers extends to verifying the credentials of manufacturers. Trustworthiness is established when manufacturers maintain transparency about their production processes, offer detailed product documentation, and provide warranties and after-sales support. Users in the field often rely on case studies and user reviews, which serve as third-party validation of the crossover's effectiveness in diverse working conditions. These reviews and studies not only validate the manufacturer's claims but also provide insights into the practical performance of the crossovers in challenging scenarios.
An experiential perspective offers invaluable insights into the real-world application of drill pipe crossovers. Field engineers emphasize the importance of routine maintenance and inspections to prevent any wear or tear from evolving into significant operational challenges. Experiences from the field underscore that proactive maintenance schedules ensure crossovers function optimally, helping to avoid unscheduled breaks that can delay projects and inflate costs. Furthermore, adaptability in using these tools across different projects without compromising structural integrity speaks volumes about their design excellence and robustness.
In concluding, the significance of drill pipe crossovers transcends their apparent simplicity. As facilitators of connectivity and communication between disparate drilling components, they epitomize the blend of engineering precision and material science. The synergy between these elements ultimately contributes to the enhanced productivity of the drilling operations. With technology and industry standards continually evolving, the role of crossovers is poised for further innovation, ensuring they remain at the forefront of efficiency solutions within the energy sector.
Recognizing the combination of expertise, experience, authoritative designs, and trustworthy practices surrounding drill pipe crossovers is essential for industry professionals seeking to optimize their operations while aligning with best practices in safety and performance standards. This holistic view not only caters to immediate operational needs but also anticipates future advancements in drilling technology, promising ever-greater efficiencies and outcomes.