In the ever-evolving landscape of oil and gas exploration, drill pipe crossover technology stands out as a pivotal component in optimizing well operations. Drill pipe crossovers facilitate the transition between different types of drill strings or tools, ensuring seamless connectivity and operational efficiency. Drawing from a wealth of industry expertise and real-world experiences, this article explores the nuances of this crucial technology while emphasizing its importance and reliability within the industry.
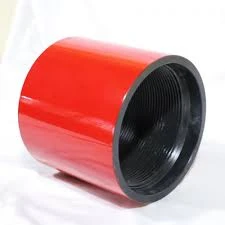
Drill pipe crossovers are an essential tool in any drilling operation, addressing the challenge of connecting pipes or tools of varying diameters and threads. These adaptors are crafted with precision to ensure they withstand the rigors of drilling conditions while maintaining a secure connection between drill strings. As drilling operations often involve various tools and devices, having crossovers that can efficiently link different components can significantly enhance the overall efficiency and safety of drilling projects.
Industry experts with years of experience underscore the significance of selecting high-quality drill pipe crossovers. The material composition and engineering design play a crucial role in their performance. Typically, crossovers are manufactured from high-strength alloy steel, engineered to endure the extreme pressures and temperatures encountered during deep drilling. The integrity of the connection reduces the risk of tool failure, thus safeguarding personnel and equipment from potential hazards.

Operational integrity hinges on the meticulous machining of threads, which requires a perfect alignment to avoid any malfunctions during drilling operations. Threaded connections are vital for two reasons they need to endure significant amounts of tension and compression, and they must provide a leak-proof seal against the milieu of drilling fluids. For operators, the expertise in managing these crossover components dictates the fluidity of the entire drilling process, influencing both effectiveness and safety.
drill pipe crossover
The effectiveness of a drill pipe crossover is further enhanced by innovative coating technologies that protect against corrosive environments, thereby extending their lifespan. Advanced coatings mitigate the risk associated with sulfide stress cracking and hydrogen embrittlement, common in aggressive drilling conditions. Through real-on-the-field tests and expert evaluations, these coatings are continually refined to heighten performance and reliability.
The trustworthiness of a drill pipe crossover also lies in rigorous quality control standards adhered to during its manufacturing process. Certifications such as ISO and API standards serve as a benchmark for quality assurance. These standards govern the design, production, and inspection processes, ensuring the crossovers meet the highest industry yardsticks. Operators rely heavily on these certifications as a badge of reliability, which is pivotal when operational goals and safety concerns are at stake.
An authoritative understanding of drill pipe crossovers is incomplete without insights into their application-specific advantages. In unconventional drilling environments, like shale or deepwater drilling, the ability to adapt quickly to different requirements without significant downtime can be a game-changer. Incorporating high-quality crossovers means minimizing disruptions, ensuring that workflow remains uninterrupted, and extraction projects stay within budgetary and time constraints.
Drill pipe crossover technology represents a blend of engineering precision and operational wisdom. Its role in achieving seamless integration within the drilling process cannot be overstated. By prioritizing quality, adhering to stringent standards, and leveraging cutting-edge protective technologies, these tools prove themselves indispensable within the drilling industry. Dependable, adaptable, and robust—drill pipe crossovers are not merely components of the drilling process; they are integral to driving operational success in challenging environments.