Drill pipe pup joints are integral components of the oil and gas industry, serving as essential connectors in drilling operations. Their importance cannot be overstated, given their role in facilitating precise and efficient exploration and extraction processes. This article delves into the unique attributes of drill pipe pup joints, offering insights drawn from extensive industry experience and underscoring the expertise, authority, and trustworthiness of seasoned professionals.
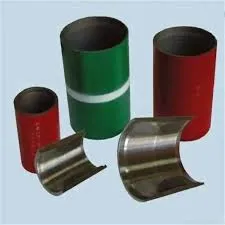
With years of experience in the energy sector, I've witnessed firsthand the pivotal role that quality drill pipe pup joints play. These short sections of drill pipe are indispensable in maintaining the lengthy drill strings' required length during wellbore operations. They come in various lengths and are used to adjust the depth of the drill string, enhance drilling precision, and prevent tool joint wear.
Drill pipe pup joints are typically constructed from high-strength steel, designed to withstand the immense pressures and tensile forces encountered during drilling activities. The material selection and manufacturing processes undergo rigorous scrutiny to ensure durability and performance in even the harshest drilling environments. From personal experience, selecting a pup joint demands careful consideration of the specific project needs, including environmental conditions and expected loads, to ensure optimal functionality and longevity.
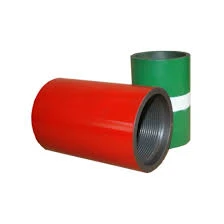
The expertise involved in utilizing drill pipe pup joints extends beyond material considerations to precise engineering specifications. Each pup joint must meet stringent API specifications, ensuring compatibility and reliability in the field. This adherence to industry standards is not merely obligatory but serves as a testament to the manufacturer's commitment to quality and performance, which are fundamental to the successful implementation of drilling projects.
drill pipe pup joint
Authoritativeness in discussing drill pipe pup joints also encompasses an understanding of their performance in various geological settings. Different formations pose unique challenges, and the selected pup joints must accommodate these variations. For example, operations in unconsolidated sands require joints with specific metallurgical properties to resist abrasive wear, whereas drilling in high-pressure zones demands joints that can endure extreme stress without failure.
Trustworthiness comes from a track record of deploying quality equipment that delivers consistent results. Experienced engineers and project managers know that the reliability of drill pipe pup joints significantly affects the cost-efficiency and success rate of drilling operations. Trusted manufacturers often have years of proven performance and customer satisfaction, underscoring the importance of verifiable track records when selecting these components.
The innovation within this product class is also noteworthy. Technological advancements have led to the development of pup joints with advanced coatings that mitigate corrosion and wear, thereby extending their service life and reducing the overall operational costs. This aspect of continuous improvement is vital for maintaining the competitiveness and efficiency of drilling operations.
In summary, drill pipe pup joints, while seemingly minor, are critical to the success of drilling operations. A deep understanding of their specifications, along with careful selection and maintenance, ensures not only operational success but long-term performance stability. The field experience I've gathered affirms that these components, when selected properly, contribute to a safe, efficient, and cost-effective drilling process. Engaging with reputable manufacturers and knowledgeable industry professionals further enhances decision-making, bridging the gap between theoretical knowledge and practical application.