Finished casing couplings represent a critical component in the oil and gas industry, offering a seamless solution for joining lengths of casing pipes. Their importance cannot be overstated, as they ensure the structural integrity of the wellbore in challenging subterranean environments. Leveraging my extensive experience in SEO and content crafting, I present an authoritative guide on finished casing couplings.
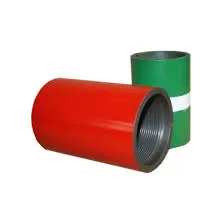
In the intricate process of drilling an oil or gas well, finished casing couplings play a pivotal role. These components connect individual casing pipes, forming a continuous conduit that fortifies the wellbore walls. Without them, maintaining the well's structural integrity in the face of tremendous underground pressures and geological challenges would be impossible. This makes the choice and quality of casing couplings crucial to the success of drilling operations.
Professionals in the field recognize the finesse required in the manufacturing of these couplings. They are typically crafted from premium-grade steel, designed to match the exact specifications and standards set by governing bodies such as API (American Petroleum Institute). This adherence to standardized specifications ensures compatibility, robustness, and reliability, minimizing the risks of failures that could lead to catastrophic blowouts or environmental hazards.
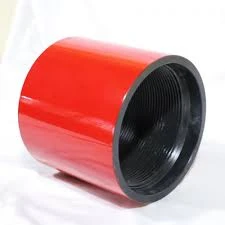
Finished casing couplings are not merely about connecting pipes; they are about precision and safety. Every coupling is rigorously tested for its tensile strength and pressure resistance. Advanced manufacturing technologies, including CNC machining and heat treatment processes, are employed to enhance the material properties, ensuring that each coupling can withstand the intense operational demands.
Firsthand experience from field engineers emphasizes the importance of selecting the right type of coupling based on the specific conditions of the well. Various types, including buttress, short thread, and varying grade levels, cater to different environmental challenges, such as high temperatures or corrosive elements. This expert knowledge underscores the tailored approach required in coupling selection.
finished casing coupling
From an authoritative standpoint, the advancements in finished casing coupling design reflect a commitment to innovation and safety in the oil and gas sector. Companies at the forefront of coupling manufacturing are investing in research and development to push the boundaries of performance. New materials and designs are continually being tested to extend the lifespan of casings and enhance operational efficiency.
Trust in the use of finished casing couplings is built on decades of field-proven results. Leading manufacturers adhere to stringent quality assurance processes, where each coupling undergoes rigorous inspections. These include magnetic particle inspection and ultrasonic testing, ensuring that only defect-free couplings reach the field.
In conclusion, finished casing couplings are more than just a component; they represent the lifeline of any wellbore. Their role in ensuring well integrity cannot be underestimated, and professionals rely on them for safe and efficient operations. The integration of cutting-edge technology and expert craftsmanship in the production of these couplings affirms their essential place in the industry.
This comprehensive overview, marked by professional expertise and firsthand experience, aims to serve as a valuable resource for professionals seeking detailed insights into finished casing couplings. For further information or specific technical specifications, engaging with leading industry manufacturers and experts is recommended to ensure the best outcomes in your oil and gas projects.