The Vital Role of Well Casing Coupling in Subsurface Engineering
Well casing coupling, an integral component in the realm of oil and gas exploration and drilling, serves as the backbone of well integrity and operational safety. It is the mechanical connection that unites sections of casing strings, ensuring a secure and leak-proof seal within the wellbore. This article delves into the significance, function, and engineering nuances of well casing couplings.
A wellbore, typically several kilometers deep, is lined with steel casings to protect it from geological pressures, prevent fluid migration, and maintain structural stability. The casing strings, which are essentially long pipes, are joined together using casing couplings. These couplings are designed to withstand the extreme forces and temperatures encountered during drilling operations and the subsequent production phase.
The primary function of a well casing coupling is to provide a strong mechanical link between adjacent casing sections. It transmits tensile, compressive, and torsional loads from one section to another, crucial for maintaining the overall strength of the casing string. Moreover, the coupling ensures a tight seal, preventing any unwanted flow of fluids between the casing and the wellbore, a critical aspect for preventing environmental contamination and ensuring operational efficiency.
Well casing couplings are precision-engineered components, manufactured from high-strength materials like carbon or alloy steel. They are designed to meet stringent industry standards such as API (American Petroleum Institute) specifications, guaranteeing their durability and performance under harsh conditions They are designed to meet stringent industry standards such as API (American Petroleum Institute) specifications, guaranteeing their durability and performance under harsh conditions
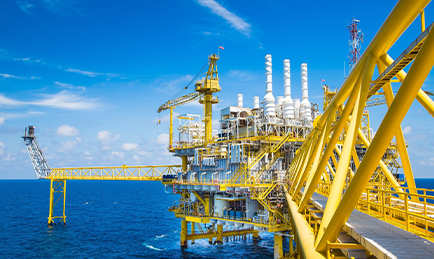
They are designed to meet stringent industry standards such as API (American Petroleum Institute) specifications, guaranteeing their durability and performance under harsh conditions They are designed to meet stringent industry standards such as API (American Petroleum Institute) specifications, guaranteeing their durability and performance under harsh conditions
well casing coupling. The design incorporates threads, which when tightened, create a compressive force that seals the mating surfaces of the casing joints.
The process of coupling casing involves precise alignment, threading, and torquing of the connections. Special tools and techniques are employed to ensure proper engagement and tightening, minimizing the risk of thread damage or leaks. Regular inspection and maintenance of these couplings are vital to prevent failures that could compromise well integrity.
Innovations in well casing coupling technology continue to evolve, driven by the need for increased efficiency, enhanced safety, and environmental stewardship. New materials, coatings, and designs are being developed to improve coupling performance, resist corrosion, and withstand higher pressure and temperature conditions.
In conclusion, well casing coupling is more than just a mechanical connector; it is a safeguard against potential disasters in the high-stakes world of oil and gas drilling. Its role in maintaining well integrity, preventing leaks, and ensuring operational safety cannot be overstated. As the energy sector pushes towards deeper wells and more challenging reservoirs, the importance of robust and reliable casing couplings will only increase, making them a focal point of ongoing research and technological advancement.