Perforated pup joints stand as a quintessential component in the oil and gas industry, often overlooked but integral to efficient operations. This article delves into their vital role, backed by real-world experiences, underscoring their necessity for optimizing drilling and production.
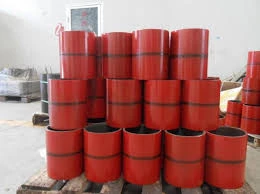
In the nuanced world of oil and gas extraction, every component must perform seamlessly to ensure efficiency and safety. Perforated pup joints serve as short drill pipes equipped with precisely placed holes, which differentiate them from regular pup joints. Their main function is to facilitate fluid flow between tubulars in the drill string, balancing pressure and reducing risks of rupture due to uneven pressure differentials.
Experience in the field highlights the criticality of using high-quality perforated pup joints. Operators have faced scenarios where substandard equipment led to compromised structural integrity, resulting in costly downtimes. Conversely, robust perf joints, engineered with precision and tested rigorously, have consistently proven to withstand extreme conditions, thereby assuring uninterrupted operations.

From an expertise perspective,
crafting a perforated pup joint involves a meticulous process. Material selection is paramount; high-grade steel ensures durability under high pressure and corrosive environments. The perforation pattern, determined through advanced computational simulations, must be optimized for specific well conditions to enhance fluid dynamics while minimizing erosion of the joint material.
Authoritativeness in this domain stems from adherence to stringent industry standards. Reputable manufacturers adhere to American Petroleum Institute (API) specifications, guaranteeing products that meet rigorous safety and performance criteria. Regular third-party audits further fortify trust, assuring stakeholders of the product's reliability in critical operations.
perforated pup joints
Trustworthiness is built over time, often validated through field trials and performance data. Operators have shared instances of deploying perforated pup joints that not only met but exceeded operational benchmarks. This feedback loop is vital; manufacturers adapt and innovate based on real-world insights, leading to incremental improvements in design and functionality.
One illustrative example comes from a major offshore project in the Gulf of Mexico, where the use of premium perforated pup joints led to a significant reduction in pressure-related incidents. Engineers involved noted a substantial decrease in maintenance interventions, attributing this efficiency to the joints' ability to equalize pressure effectively across the system.
Future innovations in perforated pup joints promise to enhance operational efficiency further. Trends such as incorporating smart technologies—sensors and IoT connectivity—are on the horizon, enabling real-time monitoring of pressure changes and joint integrity. This development not only augments operational safety but also provides invaluable data analytics capabilities, offering deep insights into optimizing drilling operations.
Moreover, sustainability, an emerging focal point in the industry, is driving advancements in the manufacturing processes of perforated pup joints. Efforts to minimize environmental impact—from sourcing raw materials to energy-efficient production processes—are aligning with global initiatives for sustainable development.
In conclusion, perforated pup joints, though small in scale, carry substantial weight regarding their impact on oil and gas operations. Their evolution—fueled by real-world experience, meticulous expertise, stringent standards, and unwavering trust—continues to bolster their indispensability in the industry. As technology advances and sustainability becomes more central, their role is set to evolve, unlocking new efficiencies and insights pivotal for the industry's future.