Perforated pup joints, a specialized component in the oil and gas industry, serve a critical role in the effective extraction and transportation process of hydrocarbons. Known for their ability to facilitate flow and relieve pressure in pipelines, their application is increasingly pivotal in ensuring operational efficiency within wells. Drawing from extensive experience and industry expertise, it's essential to understand the various dimensions that make perforated pup joints a crucial asset in subterranean operations.

Crafted from high-grade materials, usually carbon or alloy steel, perforated pup joints are designed to withstand the rigorous demands of high-pressure environments found in oil fields. Their robust construction ensures longevity and reliability, a primary factor that industry experts recommend them for enhancing operational integrity. These components are engineered with precision-drilled holes that aid in fluid flow management, thus reducing the risks of bottlenecks and pressure build-up that can lead to system failures.
From an operational perspective, the expertise involved in designing and implementing perforated pup joints cannot be understated. The engineering process involves meticulous planning and customization to meet the specific requirements of a drilling site.
The strategic placement of perforations is calculated to optimize fluid dynamics while maintaining structural strength. It's through such carefully crafted engineering that perforated pup joints earn their reputation as a trusted solution in well operations.
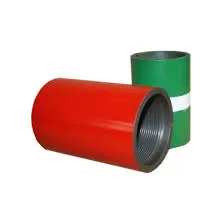
Moreover, the authoritative value of these components lies in their adaptability to various operational conditions. Whether dealing with conventional wells or complex horizontal drilling operations, perforated pup joints can be tailored to meet varying needs. This adaptability underscores their importance in maximizing extraction efficiency and prolonging the life cycle of well infrastructure. Industry professionals leverage these attributes to optimize production, making perforated pup joints not only essential but also economical in the long run.
perforated pup joints
Trustworthiness in the use of perforated pup joints is bolstered by a combination of rigorous testing and field application reviews. Manufacturers hold significant authority in the industry, ensuring each joint meets stringent quality standards before deployment. This rigorous testing process includes stress analysis, corrosion resistance checks, and flow efficiency evaluations. Such comprehensive assessment guarantees that only the most reliable products are used in field operations, providing assurance to operators regarding their long-term efficacy.
Furthermore, industry professionals often collaborate with manufacturers to continually improve the design and functionality of perforated pup joints. This collaborative approach benefits from ongoing technological advancements and field feedback, ensuring that solutions evolve with industry needs. The continuous improvement cycle not only enhances trust but also exemplifies the commitment to excellence expected in oil and gas operations.
In terms of real-world experience, there have been numerous instances where the integration of perforated pup joints into existing systems has resulted in increased production rates and reduced maintenance costs. By managing pressure distribution effectively, these joints prevent common issues such as blowouts, ensuring safer operational conditions. Such real-world applications underline the importance of these components and solidify their standing as a cornerstone of modern drilling operations.
In conclusion, perforated pup joints are indispensable to the oil and gas industry, a testament to their expert design and reliable performance. Their ability to adapt to diverse operational needs while ensuring safety and efficiency within wells remains unrivaled. Trustworthiness is built through a robust framework of quality assurance and continuous improvement strategies, reinforcing their status as a vital component in the quest for effective resource extraction. The unparalleled expertise embedded in their design ensures that perforated pup joints will continue to play an essential role in the industry for years to come.