Perforated pup joints are gaining traction in the oil and gas industry due to their innovative design and functional efficiency. These specialized components play a crucial role in well completion and production, enabling operators to enhance performance and optimize wellbore operations. Unlike standard pup joints, perforated pup joints are engineered with holes or slots that allow for controlled fluid flow, making them indispensable in situations that require pressure management and flow regulation.
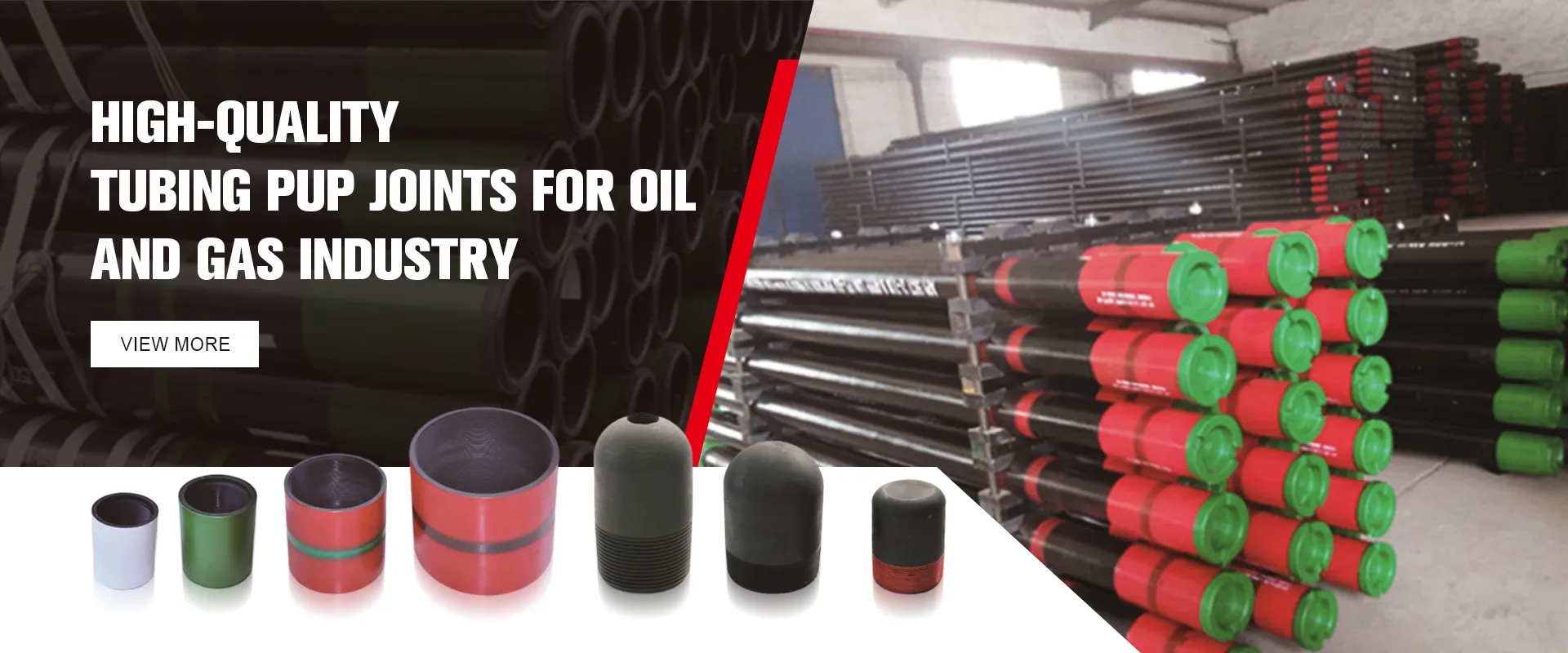
A paramount advantage of perforated pup joints is their ability to mitigate issues related to pressure differential. In traditional setups, significant pressure variation can lead to complications like sand production or mud loss, affecting well integrity and productivity. Perforated designs facilitate an even distribution of pressure along the wellbore, ensuring stable operations and reducing the risks of blowouts or formation damage.
The expertise involved in manufacturing perforated pup joints requires a deep understanding of metallurgy and fluid dynamics. Typically constructed from high-grade steel alloys, these joints must endure the harshest downhole conditions, making material integrity a priority. Industry professionals take into account factors like tensile strength, corrosion resistance, and thermal stability when designing and fabricating these components. As exploration extends to more extreme environments, the reliability of these joints is paramount, and continuous innovation is being undertaken to enhance their performance.
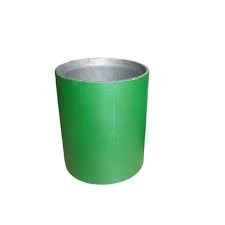
Industry insiders acknowledge the critical importance of customization in perforated pup joint applications. Each well has its unique attributes, necessitating tailored designs to match specific environmental and operational conditions. Factors such as well depth, bore diameter, temperature differentials, and expected fluid types are all accounted for, ensuring the joint serves its purpose effectively. Collaborative efforts between engineers and field operators lead to the development of bespoke solutions that not only meet regulatory standards but also optimize overall well efficiency.
perforated pup joints
The credibility of manufacturers producing these components contributes significantly to their authoritative presence in the market. High-quality perforated pup joints come with comprehensive technical documentation and testing certifications that underscore their reliability over extensive lifecycles. Periodic testing and inspections, often conducted in compliance with global standards, are mandatory practices that ensure consistent performance under dynamic well conditions.
Emerging technologies continue to influence the development and application of perforated pup joints. Digital oilfield solutions enable real-time monitoring and predictive maintenance, mitigating potential downtimes. Advanced analytics provide insights into wear and tear, operational stress, and other factors, fostering proactive management and extended asset longevity. Such advancements not only bolster the trust operators place in these solutions but also reinforce the role of perforated pup joints in complex extraction scenarios.
Trustworthiness stems from real-world performance and testimonials from field operators and engineers who have firsthand experience with these products. Anecdotal evidence suggests a substantial reduction in operational challenges when perforated pup joints are utilized correctly. They are often cited as pivotal in optimizing production rates and minimizing interventions, particularly in unconventional reservoirs where optimizing flow dynamics is crucial.
Perforated pup joints are an unsung hero in the oil and gas industry's technological toolkit, providing indispensable solutions to some of the most challenging scenarios in wellbore management. Their evolution aligns with industry needs for efficiency, safety, and sustainability, reinforcing their role as critical components in both conventional and advanced well operations. Operators investing in high-quality perforated pup joints can expect to realize significant gains in both operational reliability and economic metrics, underscoring the lasting value and impact of these innovative tools.