Petroleum tubing coupling is an indispensable component in the oil and gas industry, acting as the critical link ensuring the secure transport of resources from deep within the earth to the surface. This niche product, while often overlooked, plays a vital role in the seamless operation of oil fields and deserves keen attention for its precision and reliability.

In the competitive landscape of the oil and gas sector, the petroleum tubing coupling is revered for its precision engineering and durability. A thorough understanding of its specifications and functionalities is crucial for field engineers and procurement specialists. Made typically from high-grade steel to withstand extreme pressures and temperatures, these couplings undergo rigorous testing to meet industry standards like API 5CT. This ensures not only resilience but also guarantees operational safety, a non-negotiable in environments where failures can result in catastrophic consequences.
The selection of the right coupling can significantly impact operational efficiency. Factors like thread type—whether API or proprietary premium connections—material grade, and size are pivotal considerations. For instance, in environments with corrosive agents, couplings must be crafted from corrosion-resistant alloys to prolong the lifespan of the tubing, ensuring that the resource extraction process is not only efficient but also sustainable.
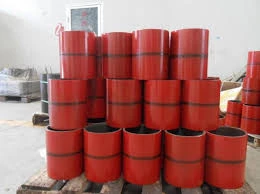
Moreover, recent advancements in coupling technology have introduced innovations like anti-galling coatings and advanced sealing mechanisms. These features enhance the connection's ability to maintain integrity under adverse conditions, thereby reducing maintenance needs and minimizing downtime. Such innovations underscore the industry's shift towards more sustainable and cost-effective solutions, essential for maintaining profitability in fluctuating markets.
petroleum tubing coupling
Expertise in the realm of petroleum tubing and coupling also extends to understanding the operational environment. For instance, deep-water drilling operations may necessitate different coupling characteristics compared to onshore projects. Geological factors, such as the presence of hydrogen sulfide or extreme pressures, demand tailored solutions to prevent leakages and ensure longevity. Thus, a coupling's design is often a collaboration between manufacturers and field experts, combining engineering prowess with practical field insights.
Trust in the coupling's performance is cultivated through comprehensive field testing and extensive quality assurance protocols. Manufacturers who invest in cutting-edge R&D and foster close relationships with end-users often find themselves at the forefront of the market, revered for their products' reliability. Their expertise reflects not only in the robustness of their products but also in the technical support and guidance they offer, underscoring their authority in the field.
Ultimately, the authoritative choice of petroleum tubing coupling is not just a matter of selecting high-quality steel or advanced threads; it's about a calculated strategy that considers lifecycle costs, field conditions, and long-term operational goals. As environmental considerations take center stage in global energy discussions, couplings that offer enhanced sealing to prevent environmental contamination are becoming increasingly vital.
With every coupling decision, stakeholders are not just investing in a component but in the continuity of their operations. In an industry where trust can impact the bottom line, the assurance of quality and performance that a coupling provides is invaluable. This makes petroleum tubing coupling not just a technical necessity but a strategic asset in the quest for energy exploration and extraction excellence.