Petroleum tubing coupling plays a critical role in the oil and gas industry, ensuring the secure connection of tubing strings in wellbores and guaranteeing the efficiency of petroleum extraction. For companies involved in hydrocarbon production, understanding the nuances of high-quality tubing couplings can significantly affect bottom lines and operational safety.

Couplings are the unsung heroes in the tube string assembly, nesting between tubing sections and maintaining the structural integrity of the string under challenging conditions. Petroleum extraction environments can be harsh, with extreme pressures, temperatures, and corrosive elements. Therefore, investing in superior tubing couplings is paramount for ensuring reliability and longevity in these adverse conditions.
In terms of expertise, the manufacturing processes of these couplings have undergone stringent advancements. Precision engineering is vital, and today, coupling manufacturers employ cutting-edge techniques, including CNC machining and advanced metallurgy, to produce couplings that meet rigorous industry standards. They are commonly made from high-grade carbon steel or premium alloys, which provide enhanced resistance against mechanical wear and environmental degradation.
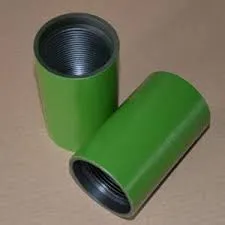
Manufacturers also incorporate robust quality control measures. These include rigorous testing procedures like hydrostatic testing, magnetic particle inspection, and ultrasonic testing, ensuring that each coupling can withstand the demands of downhole environments. The expertise of engineers and geologists in designing couplings that fulfill specific operational requirements cannot be overstated. Their role in determining the coupling's metallurgical properties and geometric tolerances ensures optimal performance in specific well conditions.
From an experience standpoint, seasoned professionals in the oil and gas industry often rely on historical data and case studies when selecting the right petroleum tubing couplings for their projects. An extensive portfolio of field-tested results guides their decisions, which have a direct implication on the efficiency and safety of oil extraction operations. The successful deployment of the correct coupling can prevent costly failures, reduce downtime, and ultimately enhance the production rate of wells.
petroleum tubing coupling
As an authoritative figure in the supply chain, a coupling manufacturer needs a deep understanding of industry-specific certifications and regulatory compliances.
API (American Petroleum Institute) certifications, such as API 5CT for casing and tubing, are crucial benchmarks. Such credentials provide trust in the market, assuring end-users that the products meet international quality and performance standards.
Coupling manufacturers must foster a relationship built on trust with their clientele. Open communication channels, coupled with transparency in manufacturing processes and delivery schedules, contribute to a trustworthy brand image. Offering extensive post-purchase support and warranty solutions also enhances brand loyalty, encouraging long-term partnerships with oil and gas operators.
Finally, technological advancements continue to innovate the petroleum tubing coupling industry. Recent developments include the integration of IoT (Internet of Things) technologies, allowing operators to remotely monitor coupling performance and predict maintenance needs, further enhancing operational integrity and reducing failure risks.
In conclusion, the critical importance of petroleum tubing couplings in the oil and gas industry cannot be underestimated. The intricate balance between engineering prowess, quality assurance, and industry expertise ensures the creation of reliable coupling products. These products underpin the structural integrity and performance of well operations, making them indispensable components in efficient petroleum extraction processes. As industry demands evolve, the continuous innovation and commitment to excellence in coupling design and manufacture will remain a cornerstone of this pivotal sector.