In the realm of petroleum extraction, tubing coupling stands out as an indispensable component ensuring the efficiency and integrity of oil and gas production. These seemingly modest devices play a critical role that goes beyond mere connectivity in tubular systems, acting as a vital link in preventing leaks and sustaining pressure in downhole operations. As oil and gas professionals navigate the complexities of drilling and production, understanding the value of quality petroleum tubing coupling becomes imperative for optimized field performance.
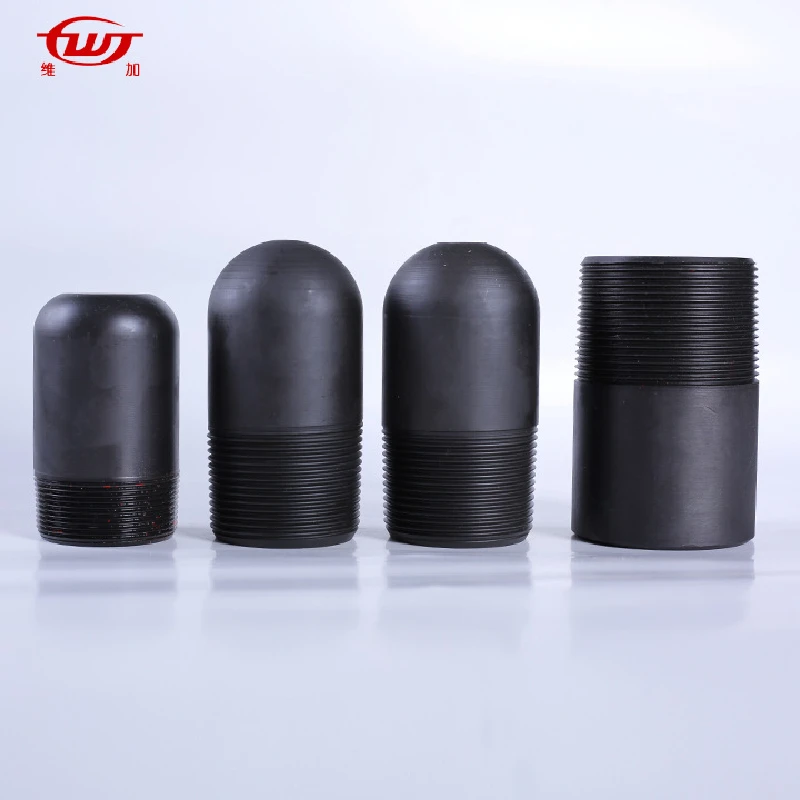
One primary aspect that distinguishes effective tubing coupling is its material composition. Manufacturers utilize high-grade alloys or carbon steel to withstand the extreme conditions found in subsurface environments. Employing materials capable of withstanding high pressures and corrosive elements ensures a long lifespan and reduces the frequency of intervention required for maintenance or replacement. This factor plays a significant role in the total cost of ownership, contributing to project sustainability and cost management.
Precision engineering is another hallmark of superior petroleum tubing coupling. The seamless integration of components is not only a mechanical necessity but a safety imperative. Every coupling is designed with threading that ensures a secure, leak-proof fit between tubular segments. This feature is critical when operating in high-pressure zones, where even minor leaks can result in costly shutdowns or environmental hazards. For onshore and offshore drilling operations, investing in such high-precision components is paramount in advancing operational safety standards.
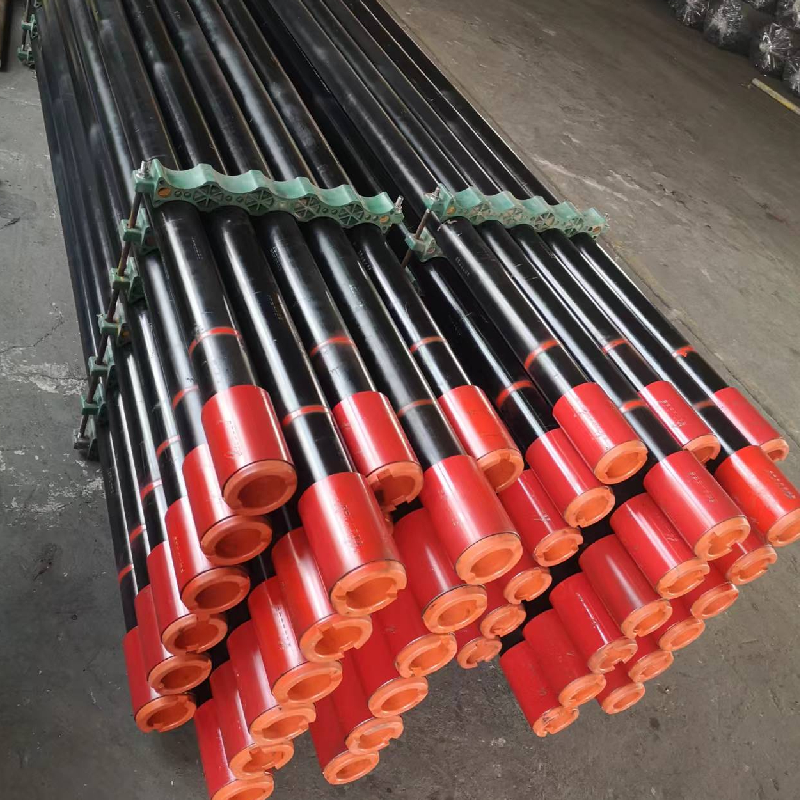
From an expertise perspective, the development and selection of petroleum tubing couplings often involve an interdisciplinary approach, combining insights from fluid dynamics, material science, and mechanical design. Engineers must account for variables such as temperature fluctuations, chemical exposure, and mechanical stress. Drawing upon this extensive knowledge base, coupling designs are constantly being refined to meet the evolving demands of modern extraction technologies, such as enhanced oil recovery (EOR) and deep-water drilling.
petroleum tubing coupling
Moreover, the authority in petroleum tubing coupling innovation rests largely with manufacturers who have established a track record of reliability and performance. Companies like Tenaris and Vallourec have become synonymous with high-quality tubular products, offering comprehensive solutions that include technical support and testing services. When selecting a coupling provider, seeking out renowned brands with a proven history of successful applications in similar operational conditions is a strategy that mitigates risk and enhances project outcomes.
Trustworthiness in tubing coupling products emerges from both empirical performance data and field testimonials. Documenting case studies where specific coupling solutions have demonstrably improved production efficiency or prolonged asset life provides substantial credibility. Furthermore, adherence to industry standards such as the American Petroleum Institute (API) specifications is a non-negotiable criterion that underpins quality assurance and builds confidence among stakeholders, ranging from engineering teams to financial investors.
As technology advances, the role of intelligent systems and IoT in monitoring coupling effectiveness is becoming increasingly prevalent. Integrating real-time data collection and analytics into tubular systems allows for predictive maintenance strategies and instant identification of potential issues. This adaptive approach enhances decision-making processes, resulting in reduced downtime and optimized resource allocation.
In conclusion, petroleum tubing coupling is more than just a functional requirement in the oil and gas industry; it is a strategic asset integral to successful drilling and production operations. Through a combination of robust material selection, expert design, authoritative manufacturing standards, and trustworthy performance data, these components support not only the mechanical success but also the financial viability and environmental stewardship of hydrocarbon extraction projects. As industry challenges continue to evolve, so too must the approach to coupling selection and application, underlining the importance of continuous innovation and learning in this critical facet of petroleum engineering.