Pipe mills are an integral part of the industrial landscape, providing essential components for a wide range of applications from oil and gas pipelines to plumbing systems and structural frameworks. A deep dive into their operation, production processes, and technological advancements reveals a fascinating blend of craftsmanship, engineering, and innovation driving this industry forward.
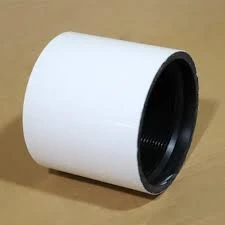
In the world of pipe production, an in-depth understanding of the various types of pipe mills is paramount. The principal categories include the seamless pipe mill, the welded pipe mill, and the continuous pipe mill, each serving distinct functions and markets. Seamless pipe mills churn out pipes without any joints, making them ideal for high-pressure applications where strength and integrity are critical. These mills primarily utilize rotary piercing techniques where a solid billet is transformed into a hollow shell by rotating and drawing it over a piercer point.
Automation and technology are at the forefront of modern pipe mills, ensuring precision and quality control that adheres to rigorous international standards. The introduction of computer numerical control (CNC) machines has revolutionized the manufacturing process by allowing for more precise cutting and shaping, significantly reducing the margin for error and material wastage. Moreover, advanced non-destructive testing methods like ultrasonic and electromagnetic assessments ensure that each pipe produced is free from defects and ready for even the most demanding applications.
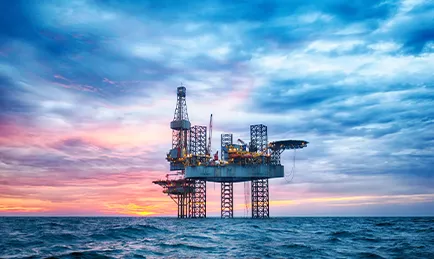
With the growing emphasis on sustainability and eco-friendly practices, pipe mills are also innovating to reduce their environmental impact. By integrating recycled steel and minimizing waste in the production process,
mills are making strides towards more responsible manufacturing. Furthermore, the incorporation of energy-efficient technologies, such as heat recovery systems and LED lighting, not only reduces the carbon footprint but also contributes to cost savings, enhancing the overall efficiency of the facility.
The role of computer-aided design (CAD) in pipe mill manufacturing cannot be understated. CAD systems enable engineers to test the design and functionality of pipes under various conditions, ensuring that the final product meets all necessary specifications and performance criteria. This design process is crucial in sectors like oil and gas, where pipelines must withstand high pressures and harsh environmental conditions. The ability to simulate different scenarios in a virtual environment allows engineers to refine and optimize designs before actual production begins, thus reducing time and costs.
pipe mill
To ensure that pipe mills remain at the cutting edge of industry standards, ongoing research and development are vital. Academic and industry collaborations are frequently seen, focusing on developing new materials and improving the resilience and durability of pipes. High-strength low-alloy (HSLA) steels and corrosion-resistant alloys are among the materials gaining traction for new pipeline projects, promising greater longevity and resistance to environmental degradation.
Emerging trends in digital technologies, like the Internet of Things (IoT) and Industry 4.0, are also making their way into pipe mills. IoT devices can provide real-time data on the operational efficiency of machinery, facilitating predictive maintenance and reducing downtime. Such technological integration ensures that production continues smoothly without unexpected interruptions, maintaining the flow of supply to meet market demands.
Safety remains a top priority in the pipe mill industry. With stringent regulations governing the handling of equipment and materials, manufacturers are investing heavily in staff training and safety protocols. Automated systems not only enhance the safety of operations by minimizing human error but also aid in maintaining a safe working environment through real-time monitoring and emergency response systems.
The pipe mill industry also plays a pivotal role in regional economic development by providing jobs and contributing to the infrastructure required for growth. As urbanization expands and the demand for energy infrastructure increases, the need for reliable and efficient pipe production will continue to rise, positioning pipe mills as crucial contributors to economic stability and development.
In summary, the pipe mill industry embodies a unique blend of traditional and modern practices, intertwined with cutting-edge technology and innovation. By focusing on quality, sustainability, and efficiency, pipe mills not only meet current industrial needs but also pave the way for future advancements. This dynamic and evolving field offers exciting opportunities for those invested in engineering, manufacturing, and the global supply chain.