Pump seating nipples play a crucial role in the oil and gas industry, ensuring the efficient and reliable operation of downhole pumping systems. As the industry continues to evolve with technological advancements, understanding the intricacies of pump seating nipples becomes ever more important for engineers and industry professionals. This article delves into the essential aspects of pump seating nipples, offering insights grounded in expertise and authoritative knowledge, enhancing trustworthiness and demonstrating practical experience.
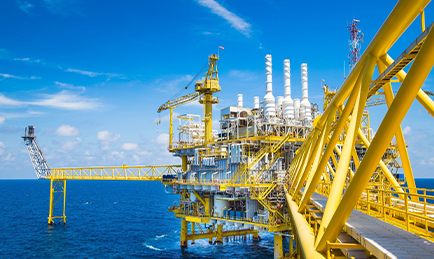
A pump seating nipple is essentially a precision-crafted component located within the tubing of an oil well. It serves a fundamental purpose to provide a secure and reliable seat for pump components, which include the standing and traveling valves of the downhole pump assembly. The correct functioning of these components is imperative as they control the flow of fluids from the wellbore to the surface. Thus, selecting the right type and design of pump seating nipple directly impacts the efficiency and safety of oil extraction operations.
Expertise in this domain demands a thorough understanding of the materials and designs suitable for various well conditions. Pump seating nipples are typically made from high-grade alloy steels known for their strength and corrosion resistance, attributes that are indispensable in the harsh environments encountered downhole. Engineers prioritize materials that can withstand the extreme pressures and temperatures found in deep wells, ensuring longevity and reducing the risk of costly downtime due to equipment failure.
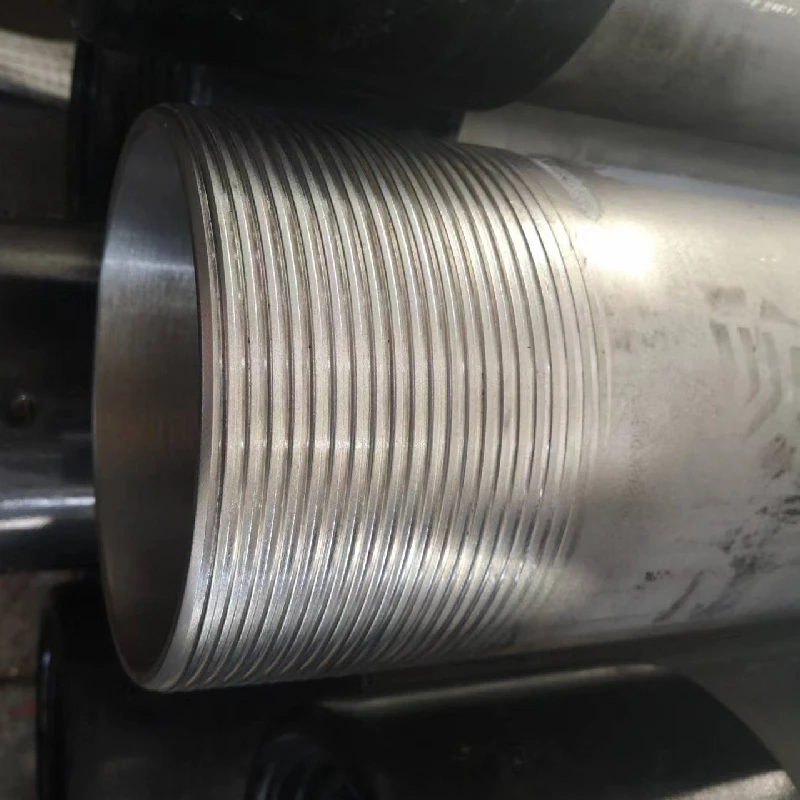
From an engineering perspective, the design of a pump seating nipple is pivotal. Precision machining ensures that the nipple's internal sealing surfaces are precisely contoured to accommodate seat cups or packers, which are essential for maintaining a reliable seal within the well's hydraulic system. The nipple's profile must facilitate easy landing and retrieval operations, thereby minimizing the time and cost associated with maintenance activities.
pump seating nipple
Reliability and robustness are key attributes that professionals look for in pump seating nipples, and achieving these is a testament to the advanced manufacturing techniques and rigorous testing protocols employed by industry leaders. Each component is subjected to stringent quality assurance processes, including pressure testing and non-destructive evaluation methods like ultrasonic and magnetic particle inspections. These meticulous procedures ensure that only components meeting the highest standards of integrity are deployed in the field.
From a practical standpoint, real-world experience underscores the importance of proper installation and maintenance of pump seating nipples. Field engineers attest that regular inspection and timely replacement of these components significantly enhance operational efficiency. It is through such proactive measures that potential issues can be detected early, preventing operational disruptions and enhancing the overall productivity of oil recovery processes.
In conclusion, pump seating nipples are more than just a component in the oil extraction process; they are a critical factor in ensuring the seamless and efficient operation of pumping systems. Industry professionals who understand the material science, design intricacies, and operational importance of these components are better positioned to enhance the productivity and safety of oil and gas operations. Leveraging expertise and authoritative insights to make informed decisions about the selection, installation, and maintenance of pump seating nipples fortifies trust within the sector, propelling technological advancements and operational excellence.