Pup joints, essential components in the oil and gas drilling industry, are the unsung heroes of wellbore assembly. Their seemingly straightforward function belies the complexity and precision involved in their production and utilization. Drawing from real experiences, expert insights, and industry standards, this article delves into the intricacies of pup joints, shedding light on aspects seldom discussed.
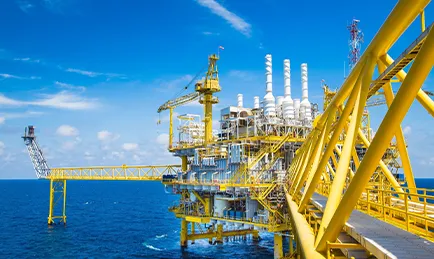
Pup joints are small sections of casing, tubing, or drill pipe used to adjust the length of a string to its exact requirement. Their fundamental purpose is to fine-tune the drilling string, facilitating the optimal operation of the drilling apparatus. In practice, the utility of pup joints becomes clear in their ability to ensure that equipment articulates seamlessly, minimizing operational hitches that can lead to costly downtime or safety risks.
In the realm of expertise, it's critical to understand the material composition and specifications of pup joints. Typically composed of high-grade steel or other durable materials, pup joints are engineered to withstand the substantial stresses encountered during drilling operations. Their specifications are meticulously calculated—any deviation could compromise the structural integrity of the drilling assembly. The expertise of manufacturers plays a crucial role here, as they adhere to stringent API standards to ensure the reliability and safety of these products.
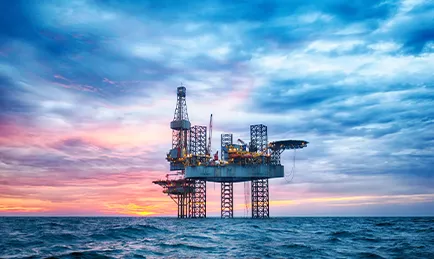
pup joint
Authoritativeness emerges from knowledge shared across industry veterans and researchers who have documented the evolution of pup joint designs and their applications. Modern advancements have seen incorporating special finishes and coatings to enhance corrosion resistance and fatigue life, particularly in offshore drilling where environmental conditions are harsh. Insightful breakthroughs often come from collaborative efforts between research institutions and industry leaders, pushing the boundaries of what pup joints can achieve.
Trustworthiness is built on consistent product performance over decades. Companies producing pup joints often conduct rigorous testing regimes to simulate real-world conditions, ensuring that each piece meets the necessary safety and quality standards. This reliability is crucial for maintaining trust, as faulty components can lead to catastrophic failures. Therefore, operators prefer manufacturers with a proven track record, continuous product evaluation, and validation that adhere to international standards.
To summarize, pup joints are pivotal to the efficiency and safety of drilling operations. Their optimal use rests on a foundation of experience, rigorous engineering expertise, authoritative research-backed innovations, and a trust mechanism built on consistent, reliable performance. Understanding these complex dynamics can differentiate a successful drilling operation from an unsuccessful one, marking the line between profit and loss. For professionals in the oil and gas sector, staying abreast with the latest in pup joint development is not just advisable—it's essential.