Pup joints are indispensable in the world of drilling operations, specifically tailored to cater to the intricate demands of the oil and gas industry. These short pieces of tubular pipe are meticulously crafted to meet stringent standards, making them a crucial component in drill strings for both onshore and offshore projects. The role of pup joints in drilling extends beyond mere connections; they are the linchpin of ensuring operational continuity and safety.
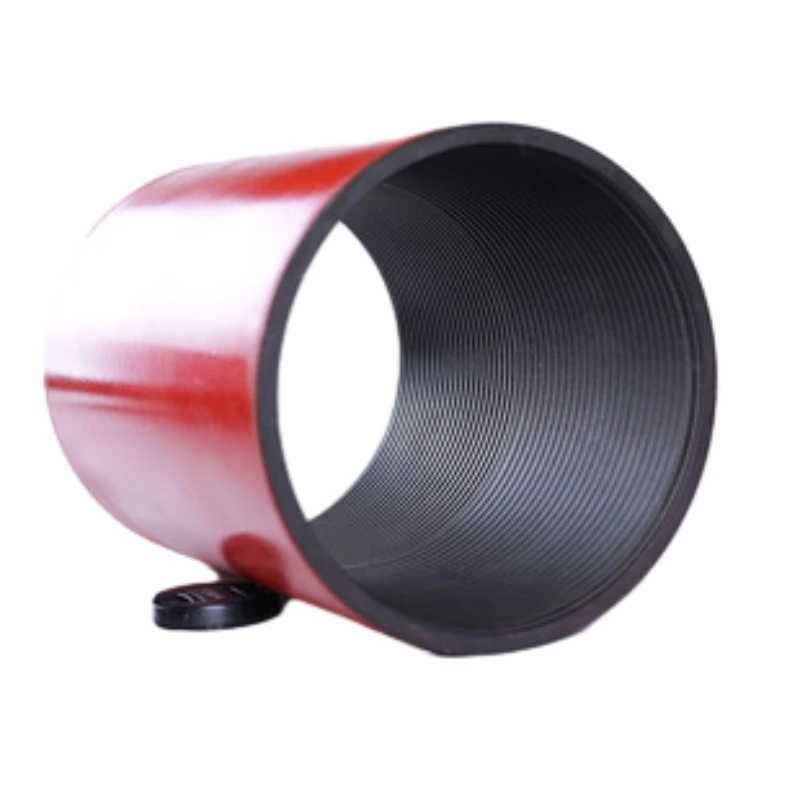
The primary utility of pup joints lies in their ability to adjust the length of the drill string, which is vital in maintaining control over pressure, ensuring proper depth alignment, and facilitating an efficient flow operation. A key aspect of pup joints is their ability to seamlessly integrate with larger segments of drill pipes and collars, providing flexibility and precision in managing the drill string's total length.
Pup joints come in various sizes and grades, designed to withstand the extreme conditions encountered during drilling operations. This adaptability ensures that they can handle high pressures and intense mechanical stress without compromising on performance. Typically constructed from high-grade steel, these joints are subjected to rigorous testing and certification processes to guarantee their reliability in the field.
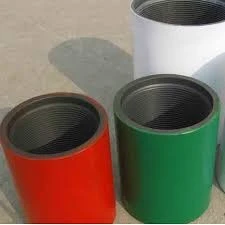
Expertise in the manufacturing and selection of pup joints is crucial. Manufacturers must adhere to stringent API (American Petroleum Institute) standards to ensure each unit's compatibility and integrity. For industry professionals, understanding the nuances of different thread types and material grades is imperative. Choosing the right pup joint is not merely about matching sizes but also about ensuring that the joint can handle specific environmental and operational challenges.
One of the hallmarks of a robust pup joint is its ability to operate efficiently under varying thermal conditions. In deep-sea drilling or Arctic operations, temperature fluctuations can pose significant challenges. The material composition and thermal treatment processes used in manufacturing pup joints are critical to maintaining their integrity in such extreme environments. This reliability extends to the prevention of corrosion, which is a common concern in offshore drilling due to saltwater exposure.
pup joint drilling
Trustworthiness and authority in the pup joint market are often established through a track record of performance and innovation. Leading manufacturers invest heavily in research and development to enhance the durability and performance of their products. By incorporating advanced metallurgy and coating technologies, these companies aim to extend the life span of pup joints and reduce the risk of operational downtime.
For drilling operations, the trustworthiness of a pup joint is ultimately validated in the field. Real-world case studies often serve as the benchmark for assessing the reliability of these components. Operators look for evidence of how particular pup joints have performed under similar conditions, often relying on testimonials and detailed performance analyses from previous projects.
Another emerging trend is the integration of smart technology within pup joints. As the oil and gas industry evolves towards more automated and digitally monitored operations, manufacturers are exploring ways to incorporate sensors into pup joints. These sensors can provide real-time data on stress loads and environmental conditions, enabling predictive maintenance and reducing the likelihood of unexpected failures.
In choosing pup joints, industry professionals must consider factors beyond mere cost. It's a decision that impacts safety, performance, and the financial bottom line of drilling operations. Therefore, collaboration with reputable suppliers and ongoing consultation with engineers and material scientists form an essential strategy for ensuring the optimal selection and utilization of pup joints in complex drilling scenarios.
Conclusively, pup joints represent a small yet critical component of drilling operations, requiring careful consideration and expertise. Their role in enhancing the efficiency, safety, and reliability of drilling cannot be overstated. As the industry continues to evolve, the next generation of pup joints will likely embody cutting-edge technology and materials, reaffirming their status as vital assets in achieving successful drilling outcomes.