In the complex world of drilling operations, selecting the right components can significantly impact performance, safety, and efficiency. Among the critical components in a drilling operation is the pup joint drill pipe, a versatile and occasionally underrated equipment piece that plays a vital role in maintaining drill string integrity and facilitating effective drilling. Drawing from extensive industry experience, we've crafted this definitive guide to help you understand the pivotal role of pup joint drill pipes and how they contribute to successful drilling projects.
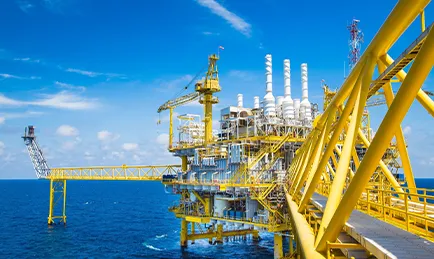
Pup joint drill pipes are short, threaded pipes used to adjust the length of the drill string. Typically ranging from a few feet to several meters, these pipes are designed to deliver precise length adjustments, ensuring the drill string fits perfectly with the drilling rig's operational parameters. Leveraging the right pup joints allows drilling operators to maintain optimal drill string lengths, which is crucial for reducing stress, improving ECD (Equivalent Circulating Density), and achieving efficient wellbore pressure management.
One of the core aspects enhancing the effectiveness of pup joint drill pipes is their adaptability. In scenarios where the target depth is close but not perfectly aligned with standard pipe lengths, these components can be inserted to achieve the desired string length. This adaptability minimizes the need for custom-length pipes and supports rapid field adjustments, often making the difference between maintaining drilling schedules and costly downtime.

The engineering of pup joint drill pipes is a testament to their significance. Manufactured to stringent industry standards, and usually from high-grade alloy steels, they offer considerable strength and reliability. Their design ensures compatibility with other drill string components, facilitating seamless integration. This compatibility is critical in high-pressure and high-temperature (HPHT) environments, where any failure in the drill string could lead to catastrophic results.
pup joint drill pipe
Pup joint drill pipes not only bring about operational flexibility but also contribute to cost efficiency in drilling programs. By using these joints, operators can minimize waste, particularly in scenarios necessitating specific string lengths, thus avoiding the financial implications of procuring custom piping solutions. Alongside reducing overall material costs, the strategic use of pup joint drill pipes aids in minimizing equipment wear, leading to longer maintenance intervals and enhanced operational uptime.
What's more, the expertise involved in choosing the right pup joint is paramount. Experienced drilling engineers understand the nuanced impact of each anatomy within the drill string. Variables such as tubing size, environment, and the mechanical properties of materials used in pup joints call for a mix of scientific knowledge and operational acumen. Every choice contributes to overall string integrity and the success of the well drilling.
Another vital factor is the continual advancement in pup joint technology. The advent of enhanced metal treatments, such as nitriding and carbonizing, increases the lifespan and resilience of these components, even under extreme conditions. These innovations further underscore the importance of staying abreast of technological advances to ensure optimal equipment performance and reliability.
In conclusion, the strategic deployment of pup joint drill pipes in drilling operations embodies a fusion of expertise, technological sophistication, and operational foresight. By ensuring the correct length and integrity of the drill string, pup joints facilitate efficient and secure drilling operations. As engineering standards continue to evolve, keeping informed on the latest advancements and best practices around pup joint drill pipes is imperative for industry professionals intent on optimizing their exploratory and development projects. Through blending experience with continual learning, operators will continue to unravel new possibilities, enhancing both the efficacy and safety of drilling endeavors worldwide.