Pup joints and drill pipes are critical components in the oil and gas industry, serving as essential tools in drilling operations. These components play vital roles in ensuring efficient and safe extraction of resources from subterranean environments. This article delves into the intricacies of pup joint drill pipes, offering insights from industry experts and backed by years of practical experience to provide a trustworthy perspective on these indispensable tools.
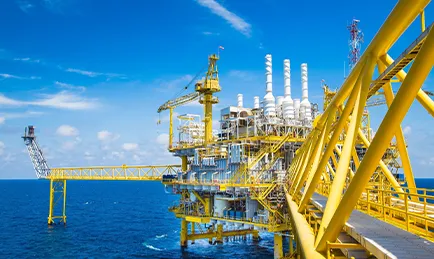
Pup joints are shorter sections of drill pipe, typically available in lengths ranging from 2 to 12 feet. They are primarily used to adjust the length of the drill string, allowing for precise modifications to accommodate various drilling operations. Pup joints are pivotal in situations where specific length adjustments are required, particularly in deviated or directional drilling operations. They aid in achieving the desired depth and ensure the drill bit reaches the intended target accurately.
Drill pipes, on the other hand, are the backbone of any drilling operation. These robust, tubular sections are tasked with transmitting torque and rotation from the drilling rig's top drive to the drill bit at the bottom. Drill pipes are designed to withstand extreme conditions, including high pressure and high temperature (HPHT) environments common in deep-well drilling. They are fabricated with strict adherence to industry standards to ensure durability, flexibility, and resilience against harsh subsurface conditions.
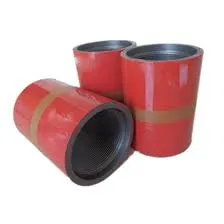
When selecting pup joints and drill pipes, several factors must be considered to ensure optimal performance. Material selection is paramount; high-grade steel, such as X95 and G105, is commonly used due to its excellent tensile strength and resistance to corrosion and fatigue. Additionally, thread connections in both pup joints and drill pipes must be meticulously chosen and inspected to avoid any operational failures arising from thread wear or breakage. Premium thread connections such as API connections and proprietary threads offer enhanced resistance to torque-induced damage and superior sealing capabilities.
Industry experts advocate for regular maintenance and inspection regimes as crucial practices to extend the lifespan and maintain the structural integrity of pup joints and drill pipes. Implementing nondestructive testing (NDT) methods, such as ultrasonic testing and magnetic particle inspection, can identify potential defects or areas of fatigue before they escalate into serious issues. Moreover, adopting innovative technologies like drill pipe condition monitoring systems provides real-time data, enabling preemptive maintenance and reducing downtime.
pup joint drill pipe
Recent advancements in drilling technology have also led to the development of specialized coatings and surface treatments for pup joints and drill pipes. These innovations aim to minimize friction, prevent corrosion, and enhance the wear resistance of the pipes, thus contributing to longer operational lifespans and improved overall efficiency. Furthermore, exploration into composite materials for drill pipes presents exciting prospects for enhanced performance and reduced weight, promising significant savings in operational costs and energy consumption.
An authoritative perspective on pup joint drill pipes recognizes the critical importance of adherence to safety protocols and industry regulations. Effective training and certification programs for drilling personnel ensure that operators are well-versed in the nuances of handling and maintaining these components. Compliance with globally recognized standards such as API, ISO, and ASME is fundamental to securing the safety and reliability of drilling operations.
Trustworthiness in the context of pup joint drill pipes derives from leveraging expertise, sharing real-world experiences, and building a knowledge-based approach that emphasizes transparency, quality assurance, and continuous improvement. Engaging with seasoned professionals and reputable manufacturers who provide detailed product documentation and exemplary customer support is essential in fostering trust within the industry.
In conclusion, pup joint drill pipes are indispensable elements that significantly influence the success of drilling operations. By emphasizing high-quality materials, adhering to rigorous inspection protocols, embracing technological advancements, and committing to safety and regulatory compliance, the oil and gas industry can harness the full potential of these critical components. Through shared expertise and a commitment to trustworthy practices, operators and stakeholders can navigate the challenges of modern drilling environments with confidence and precision.