In the intricate world of oil and gas, every component, no matter how small, plays a vital role in ensuring the seamless and safe extraction and transportation of resources. Among these components, the pup joint stands out as a crucial, though often overlooked, element. A pup joint is a short section of pipe, typically used to adjust the length of tubular strings, ensuring precise and efficient flow management in complex drilling operations.

The primary purpose of pup joints in oil and gas operations is to fine-tune the length of the drill string or tubing. This adjustment capability is essential for positioning the drill bit accurately and for ensuring optimal flow dynamics in the wellbore. Precision in length adjustment is pivotal in achieving seamless continuity in operations, preventing misalignment that could cause operational inefficiencies or even equipment failure.
Pup joints are crafted from high-quality materials to withstand the harsh environments of drilling operations. Typically forged from carbon steel or other high-strength alloys, these robust components are designed to endure extreme pressures and corrosive conditions. This durability ensures they remain dependable throughout the demanding lifespan of drilling projects, thereby reinforcing trust in their performance among industry professionals.
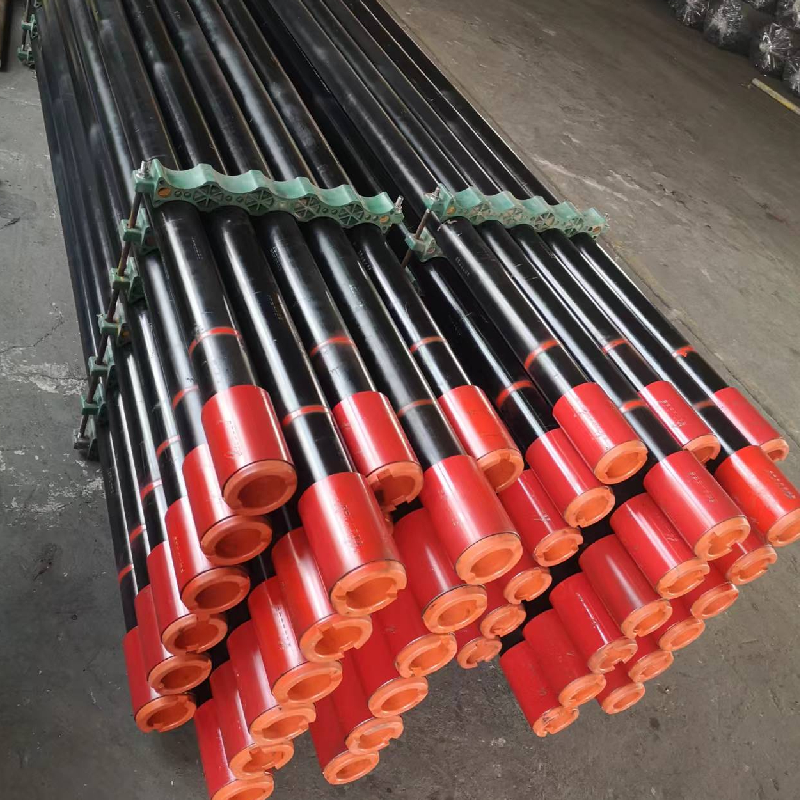
What sets pup joints apart is their versatility and adaptability. With varying lengths and thicknesses, they cater to specific project requirements, thus providing customized solutions for diverse drilling scenarios. This adaptability not only enhances operational efficiency but also provides engineers and technicians the flexibility to tackle unique challenges presented by different geological formations or project specifications. Such versatility underscores the expertise involved in employing these components in the field.
In discussing the technical expertise surrounding pup joints, it is essential to delve into the specific threads and connections that facilitate their integration into existing systems. The precision engineering of these connectors ensures leak-proof joins, preventing costly oil leaks and minimizing environmental impact. Professionalism in threading and connection crafting positions pup joints as indispensable tools for maintaining system integrity and fortifying operational trust in oil and gas endeavors.
pup joint oil and gas
Expert installation and maintenance of pup joints are paramount to maximizing their effectiveness and extending their lifespan. Regular inspections and timely maintenance, undertaken by skilled professionals, help in identifying potential wear and tear. This proactive approach ensures sustained system integrity and reliability, factors that are invaluable when considering the high stakes of oil and gas production. Industry veterans often emphasize the importance of sustained training and upskilling of personnel responsible for handling these critical components, promoting an environment of continuous learning and adaptability.
The authoritative nature of pup joint applications in oil and gas is highlighted by the stringent industry standards and certifications they must meet. Compliance with international standards such as API (American Petroleum Institute) specifications guarantees their reliability across global operations. This adherence to recognized standards ensures that they meet the highest benchmarks of quality and safety, fortifying their authoritative status within the industry.
The effectiveness and trustworthiness of pup joints in the field are underscored by decades of proven performance. Operators across oil and gas sectors frequently testify to their resilience and efficiency, which are critical to the success of challenging drilling projects. This enduring trust is a testament to the continuous innovations and refinements that manufacturers invest in, reflecting their commitment to excellence and reliability.
In essence, pup joints in the oil and gas sector embody a synergy of precision engineering, versatile functionality, and unwavering reliability. Their role, while subtle, is indispensable in orchestrating the complex symphony that is modern hydrocarbon extraction. As such, they emerge not just as tools, but as partners that drive the industry forward, ensuring operations remain both effective and sustainable amidst evolving challenges.