Pup joints, essential components in the oil and gas industry, serve as short pieces of pipe used for adjusting the length of tubular strings.
Understanding their specifications is crucial for operational efficiency and safety. With decades of industry experience, experts emphasize the importance of precise manufacturing and reliable use of these small, yet significant, components.
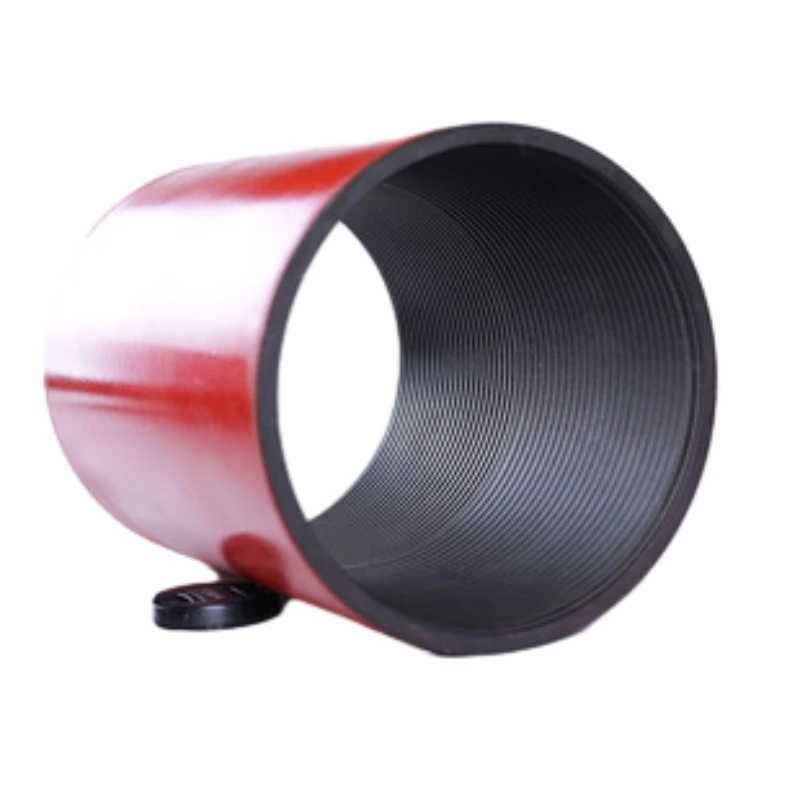
Pup joints come in a variety of lengths and are fabricated from high-grade steel to withstand the demanding environments of oil and gas extraction. The typical lengths range from 2 to 12 feet, although custom specifications are often available to meet unique operational requirements. The steel used usually conforms to rigorous industry standards like API 5CT and is treated with processes such as quenching and tempering to enhance its mechanical properties, ensuring durability under high-pressure and high-temperature conditions.
In terms of connection types, pup joints are frequently equipped with threading that matches the rest of the drilling assembly. API thread designs, such as EUE (External Upset Ends) or NUE (Non-Upset Ends), are prevalent, each serving a specific purpose. EUE connections are typically favored for their enhanced leak resistance due to the forgiving nature of their larger thread profiles, while NUE connections are chosen for configurations where a slimmer profile is needed. Choosing the correct threading is vital to safeguard against connection failures that could lead to operational downtime or environmental hazards.
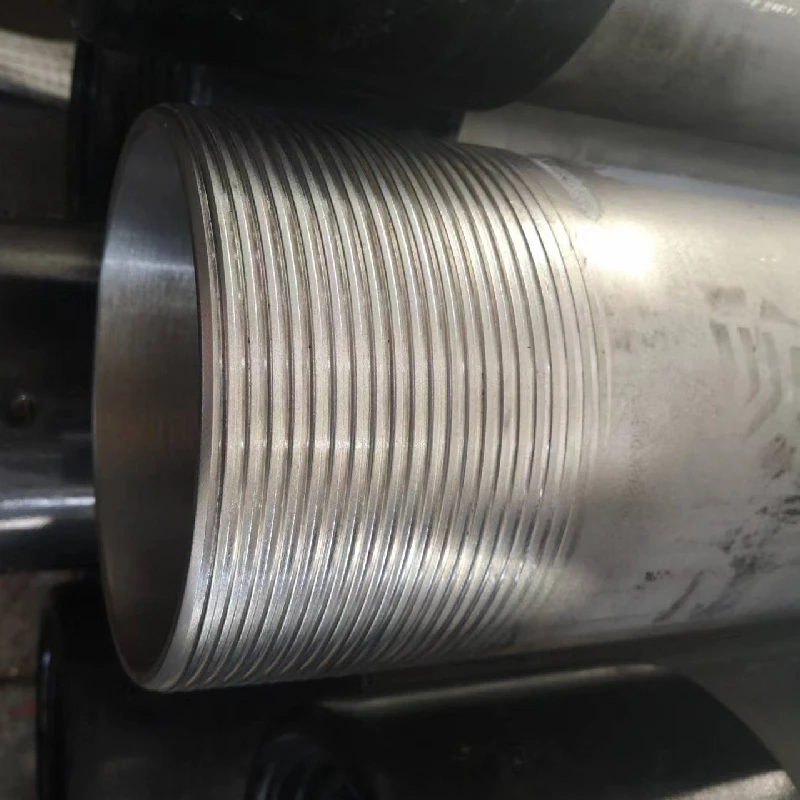
When it comes to industry expertise, an authoritative understanding of pup joint specifications extends beyond simple dimensions and materials. It involves a comprehensive approach to quality control throughout production. Each pup joint must undergo rigorous testing, including hydrostatic testing, non-destructive testing (NDT) methods like ultrasonic testing or magnetic particle inspection, and threading gauging to assure conformity with specification standards. This multi-faceted testing process ensures each pup joint can withstand the stresses encountered during operations without compromising safety and efficiency.
pup joint specifications
Trustworthiness in pup joint production also involves adopting best practices in production and logistics, ensuring that products are manufactured within certified facilities and delivered promptly. The supply chain for pup joints must be robust and efficient, utilizing top-tier quality management systems certified under standards like ISO 9001. Manufacturers must maintain meticulous documentation, providing traceability and transparency, which empowers customers to verify the quality and origin of the components they purchase.
Furthermore, it's important that operational staff are trained expertly in the correct handling and installation of pup joints to avoid accident-induced damages. Proper storage and handling practices are also crucial; pup joints should be stored in a clean, dry environment to prevent corrosion and must be handled with care to avoid mechanical damage or threading issues.
In conclusion, understanding the specifications of pup joints involves a detailed look at material choices, design standards, and quality assurance processes that combine to provide reliable performance in demanding drilling applications. This intricate knowledge backed by real-world experience ensures that these critical components meet the highest standards of safety and efficiency, enhancing trust and operational success in the energy extraction industry.