Pup joints stand as a critical component in the oil and gas industry’s arsenal, serving to connect drill strings, production tubing, and casing to facilitate smooth drilling operations and optimal resource extraction. Understanding pup joint specifications is paramount for professionals aiming for efficiency and safety in their drilling operations.
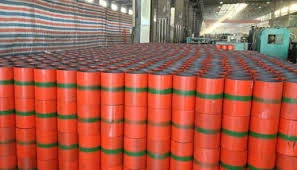
To delve into the specifications of pup joints, one must begin with an appreciation for their design, materials, and applicable standards. Typically, pup joints are short lengths of pipe—generally ranging from two to twelve feet in length—fabricated to bridge gaps within drill strings or casing structures. They are instrumental in ensuring correct alignment and spacing of the downhole equipment, thus optimizing drilling and production processes.
Material selection forms the backbone of pup joint specifications. The choice of material often hinges on the environment in which the joint will be employed. Pup joints are commonly manufactured from high-strength steel alloys which are capable of withstanding the significant pressures and corrosive environments encountered in subterranean drills. Grades like L80, P110, and N80 are frequently utilized, each offering distinct mechanical properties catered to specific operational needs. The selection between these grades is often dictated by the anticipated well pressure and the chemical composition of the reservoir.

Another pivotal aspect of pup joint specifications is the threading. The threading type can significantly influence the ease of installation and the integrity of the drill string assembly. API (American Petroleum Institute) standards often serve as the benchmark in this realm, with connections such as BTC (Buttress Threaded Connection) and EUE (External Upset End) being widely implemented. These standardized connections ensure compatibility across different components and manufacturers, fostering seamless integration within larger drilling systems.
The length and wall thickness are additional specification dimensions that drilling engineers must carefully consider. The choice of wall thickness, for instance, will impact the pup joint’s ability to withstand axial loads and bending stresses. Engineers must balance the wall thickness to enhance durability while minimizing additional weight that could compromise operational efficiency.
pup joint specifications
For any company prioritizing operational coherence, adhering to the API Specification 5CT or ISO 11960 standards for casing and tubing pup joints is non-negotiable. These standards provide comprehensive guidelines on material properties, testing methodologies, and dimensional tolerances, thus ensuring that pup joints meet industry benchmarks for safety and performance.
A lesser highlighted but equally critical specification aspect is the coating or finishing applied to pup joints. Advanced coatings provide an additional defense against harsh chemical environments, extending the service life of the joints and reducing the risk of costly operational downtimes. Options such as zinc phosphate or manganese phosphate coatings are among industry standards that significantly improve rust and corrosion resistance.
Expertise in pup joint specification is not merely an exercise in ticking boxes. It requires a nuanced understanding of both the technical demands and environmental challenges specific to each drilling site. Engineers often rely on a blend of empirical data, field experience, and emerging technologies to fine-tune these specifications. Real-world trials and rigorous testing protocols further consolidate the trustworthiness and reliability of pup joints in active field operations.
In conclusion, maximizing the efficiency and safety of drilling operations is intrinsically linked to the precise specifications of pup joints. As such, industry professionals must continually update their understanding of materials, design standards, and technological innovations pertaining to pup joints. A thorough grasp of these factors not only enhances operational efficacy but solidifies a company’s authoritative position in the competitive domain of oil and gas exploration. Thus, pup joints are far more than mere connectors; they stand as indispensable elements in the machinery of energy production.