Seamless pipes are a staple in various industries, known for their strength, durability, and versatility. Their production involves intricate processes that distinguish them from welded pipes. In this piece, built on the cornerstone principles of experience, expertise, authoritativeness, and trustworthiness, we delve into the nuances that make seamless pipes indispensable.

Seamless pipes, unlike their welded counterparts, are manufactured without any welded seams, which grants them superior strength and reduces the risk of failure under pressure. This feature alone explains their vast application across demanding industries such as oil and gas, power generation, and petrochemicals. The reliability of seamless pipes stems from their manufacturing process, which involves the extrusion of a solid billet of steel through a piercing rod, creating a hollow tube without any seams. This results in a uniform structure, providing consistent mechanical properties along the entire length of the pipe.
In terms of experience, industries have repeatedly turned to seamless pipes when precision and reliability are non-negotiable. Hydroelectric plants, for instance, utilize miles of seamless pipes within their infrastructure, where the pipes' ability to withstand high pressure and resist corrosion directly correlates to operational safety and efficiency. The oil and gas sector also provides extensive validation of seamless pipes, relying on them to transport critical resources through terrains and climates that present unique challenges.
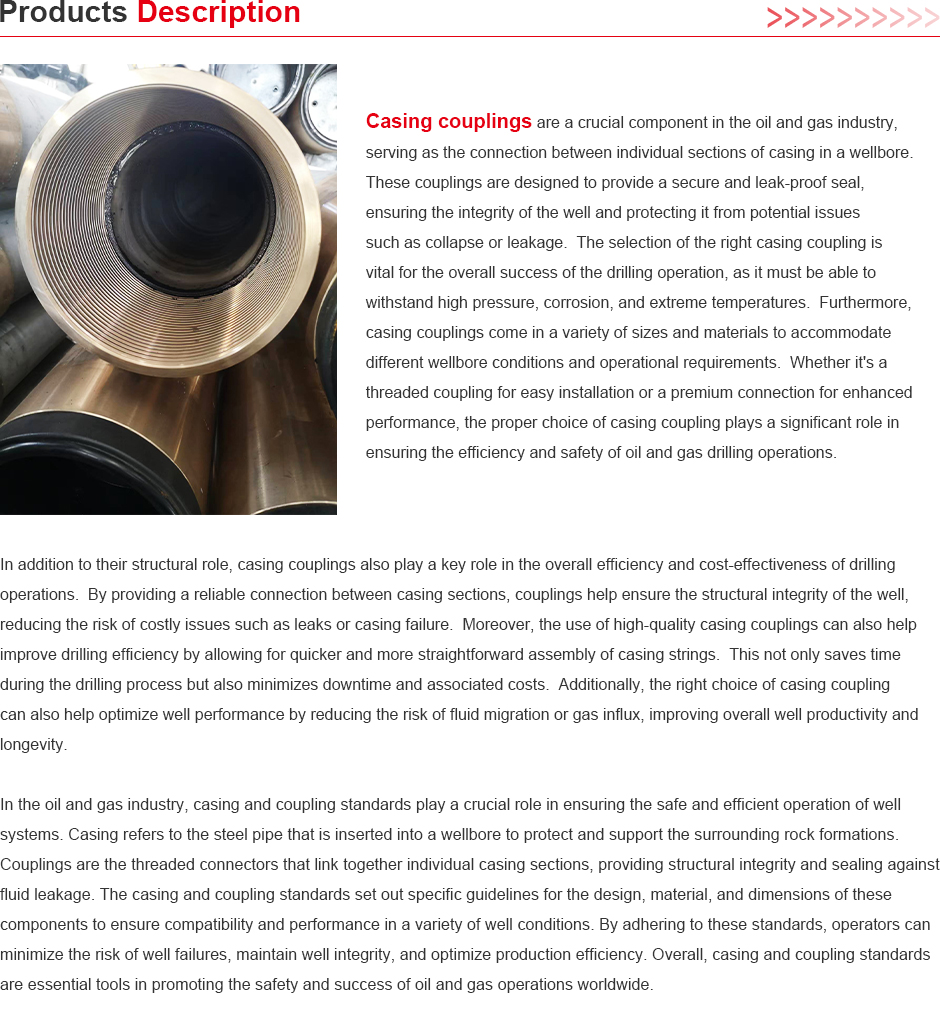
From an expertise standpoint, one must consider the specific standards and regulations surrounding the use of seamless pipes in different applications. For instance, the American Petroleum Institute (API) outlines specific grades and specifications necessary for pipes used in oil and natural gas applications, ensuring that these materials can withstand extreme temperatures and pressures. Furthermore, seamless pipes are often subjected to rigorous non-destructive testing techniques such as ultrasonic testing and radiographic inspection. These tests ensure that no internal flaws could compromise the pipe's integrity, thereby certifying their quality and performance.
seamless pipe
Authoritativeness on the subject of seamless pipes is reinforced by ongoing research and development by leading manufacturers and academic institutions. Continuous innovations aim to enhance the quality of materials and the efficiency of production processes. Specialized heat treatment processes, for instance, have been developed to further improve the mechanical attributes of seamless pipes, enabling them to meet evolving industrial demands. Moreover, the development of advanced coatings that provide additional protection against environmental factors underscores the commitment to optimizing the lifespan and reliability of seamless pipes.
Trustworthiness is vital when selecting seamless pipes for critical applications. Reputable manufacturers adhere to stringent quality control protocols, which include not only meticulous inspection of the raw materials but also comprehensive monitoring throughout the production process. Third-party certifications and customer testimonials further cement the credibility of these products. Buyers are encouraged to scrutinize product documentation and clearly understand any certifications that accompany the pipes they are considering, ensuring conformity with industry standards and specific project requirements.
Conclusively, the essence of seamless pipes lies in their robust construction and reliable performance across various demanding applications. Their inherently strong and uniform composition, proven through decades of industrial use, ensures they remain a trusted choice for engineers and project managers who prioritize safety and efficiency. Seamless pipes remain an exemplar of industrial engineering excellence, underlining the criticality of selecting the right product for the right application while upholding the highest standards of quality and reliability.