Seamless tubing couplings are pivotal components in various industries, notably the oil and gas sector. Their role in ensuring secure, leak-proof connections is indispensable. These small yet crucial devices connect lengths of pipe to form extensive networks required for transporting fluids efficiently. To grasp the significance of seamless tubing couplings, it's vital to understand their applications, benefits, and why they are considered superior to their welded counterparts.
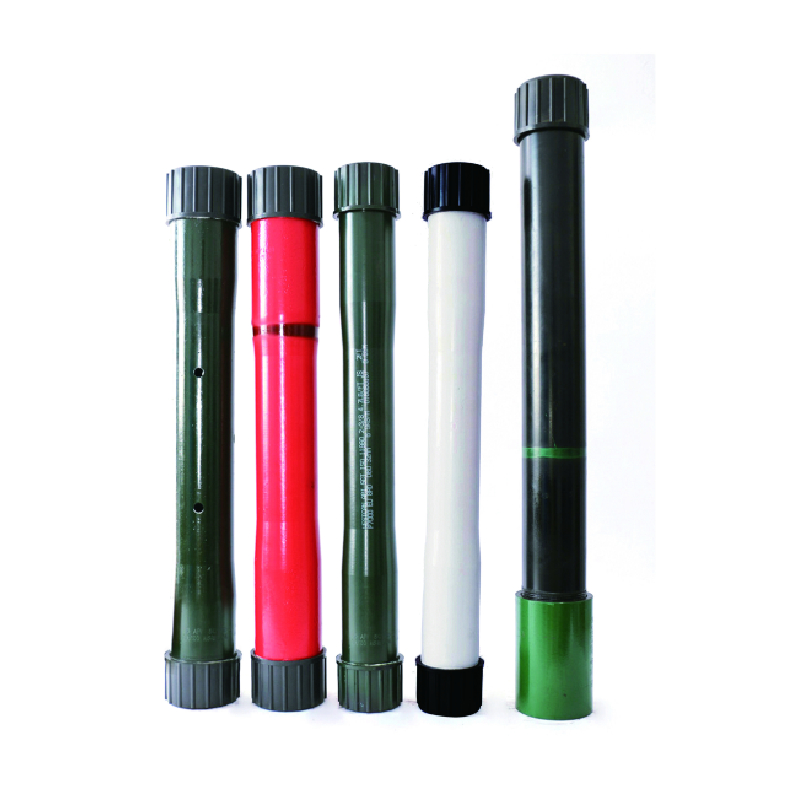
Seamless tubing couplings are predominantly utilized where the utmost precision and strength are required. Industries such as oil and gas, petrochemical, and power generation rely heavily on these components for their pipeline systems. The absence of a welded seam in seamless tubing couplings minimizes the risk of defects and weaknesses, which can be a critical advantage in high-pressure or high-temperature environments. This inherent strength is a byproduct of the manufacturing process, where the tubing is drawn from a solid billet, devoid of welding seams that could potentially compromise the integrity of the joint.
The seamless nature of these couplings contributes to their durability and longevity. Manufacturing these components involves complex processes such as piercing, extrusion, or rotary rolling, resulting in a product that can withstand significant stress and strain without failure. This robustness is particularly beneficial in adverse environments, where materials are regularly exposed to corrosive substances or extreme temperatures. Companies seeking to minimize maintenance costs and enhance the reliability of their operations often prioritize seamless tubing couplings due to their extended service life and lower propensity for leaks.
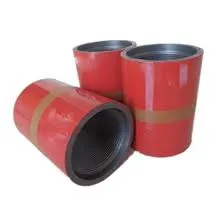
Moreover, seamless tubing couplings offer superior flow characteristics compared to their welded counterparts. The seamless surface ensures a smooth internal passage, reducing turbulence and pressure drop within the pipeline system. This efficiency leads to optimized fluid transport and reduced energy costs for pumping. In industries where fluid dynamics play a critical role, such as chemical processing or hydraulic applications, the seamless design can significantly impact operational efficiency and cost-effectiveness.
seamless tubing coupling
The expertise required to manufacture these high-precision components can't be overstated. Cutting-edge technology and stringent quality control are necessary to ensure that each coupling meets rigorous industry standards. Professionals in this field must possess a deep understanding of material sciences and engineering principles to deliver products capable of performing in demanding conditions. Companies that manufacture seamless tubing couplings invest heavily in research and development to stay ahead of industry requirements and innovations, often driving progress and setting new benchmarks for quality and reliability.
One of the key factors that mark a trustworthy seamless tubing coupling manufacturer is their certification and compliance with international standards. Certifications such as ISO, API, and ASTM are indicators of a commitment to quality and consistency. Furthermore, reputable companies often provide detailed documentation and testing results for their products, ensuring transparency and fostering trust among clients. In critical applications where failure is not an option, partnering with a manufacturer that adheres to the highest standards of quality and safety is paramount.
In conclusion, seamless tubing couplings represent an essential element in the infrastructure of numerous industries. Their ability to provide safe, reliable connections without the weaknesses associated with welded seams makes them invaluable. The commitment to excellence in their production highlights the expertise and authority of manufacturers in delivering products that consistently perform under pressure. Trust in seamless tubing couplings is not just a matter of preference but a prerequisite for ensuring the seamless operation of complex industrial systems. As industries continue to evolve and demand higher performance from their components, seamless tubing couplings will undoubtedly remain a cornerstone, driving efficiency, and reliability in the systems they support.