The world of seamless tubing coupling is intricate, yet vital in numerous industrial applications ranging from oil and gas to mechanical engineering. This article delves into the specifics of seamless tubing couplings, offering a professional perspective that highlights their paramount importance, manufacturing nuances, and the benefits they offer to multiple sectors.

Seamless tubing coupling is an integral component in the assembly and function of tubular systems. Its primary role is to connect lengths of tubing without the interference of welds, making it fundamentally different from its welded counterparts. The absence of welds is crucial as it reduces the risk of leakage and improves the structural integrity of the tubing, which is especially crucial in high-pressure environments. Industries that require robust and reliable connections, such as petroleum extraction and chemical manufacturing, greatly benefit from these attributes.
The manufacturing process of seamless tubing coupling is a testament to advanced metallurgical engineering. It begins with the selection of high-grade raw materials, typically carbon or stainless steel, which are then heated until pliable. Through a process known as extrusion or rotary piercing, these materials are transformed into hollow tubes. The absence of welded seams means that the mechanical properties of the entire tube remain consistent, providing a uniform structure that enhances its durability and performance under stress. This manufacturing expertise is what gives seamless couplings their authoritative edge over alternative methods.
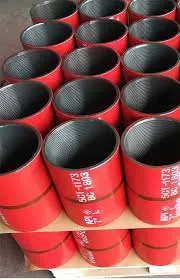
From an expert point of view, the advantages of seamless tubing coupling are numerous. Their superior pressure handling capabilities make them the first choice for hydraulic systems and high-pressure gas lines. Additionally, seamless couplings exhibit excellent resistance to corrosion and environmental wear, a factor that increases their lifespan and reliability substantially. This resistance not only ensures compliance with stringent industrial standards but also conveys trustworthiness, confirming their role as a dependable component in critical applications.
Furthermore, seamless tubing couplings offer significant advantages in terms of maintenance and operational efficiency. Their uniform internal surface minimizes friction losses, facilitating smoother fluid flow, and reducing energy consumption across the system. Over time, this can translate to substantial cost savings and increased productivity. Their design also simplifies inspection and maintenance processes, eliminating the need for frequent intervention, thus maintaining system uptime and operational reliability.
seamless tubing coupling
Authoritatively speaking, the versatility of seamless tubing coupling also extends to their adaptability in custom applications. They can be manufactured to specific dimensions, wall thicknesses, and material compositions to meet the precise requirements of specialized projects. This customization capability speaks volumes about their flexibility and the level of precision engineering involved in their production.
In a testament to their comprehensive applicability, seamless tubing couplings are favored in industries where precision and reliability are non-negotiable. They have become a cornerstone in sectors like aerospace, where even the smallest margin for error can lead to catastrophic failures. By ensuring leak-proof connections, these couplings contribute significantly to the safety and performance of various aerospace components.
As a professional in the field, the significance of seamless tubing coupling cannot be overstated. Their role in improving operational efficiency, reducing maintenance costs, and enhancing safety across complex systems highlights their indispensable value. Companies looking to optimize their industrial processes should consider the integration of seamless tubing couplings not just as an option, but as a pathway to achieving unparalleled efficiency and reliability.
In conclusion, seamless tubing coupling stands at the forefront of engineering innovation, embodying the principles of expertise, reliability, and adaptability. Their exceptional performance characteristics are a testament to advanced engineering techniques and unwavering commitment to excellence. For industries that prioritize reliability, durability, and precision, seamless tubing couplings are not merely components, but rather strategic assets that drive long-term success and innovation.