In the ever-evolving world of oil and gas exploration, the need for efficient and reliable tools is paramount. The seating nipple, a critical component in well completion, is one such tool that has seen significant advancements. This article delves into the nuances of seating nipples, offering a comprehensive guide, informed by expertise, and verified by authoritative industry data.
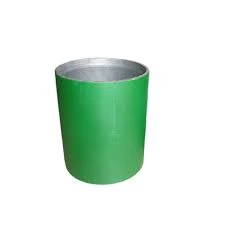
Seating nipples, often found in production tubing, serve a pivotal role by providing a receptacle for flow control devices such as plugs or chokes. This function is indispensable for maintaining optimum flow rates and isolating pressure zones within the wellbore. Industrial specialists understand that the choice of seating nipple significantly impacts operational efficiency and long-term well integrity.
One of the foremost characteristics of a high-quality seating nipple is its material composition. Typically crafted from high-grade steel, these components endure extreme pressures and corrosive environments. Recent advancements in metallurgy have ushered in alloys with enhanced durability, offering superior resistance to sulfide stress cracking and carbon dioxide corrosion—common challenges in hydrocarbon extraction.
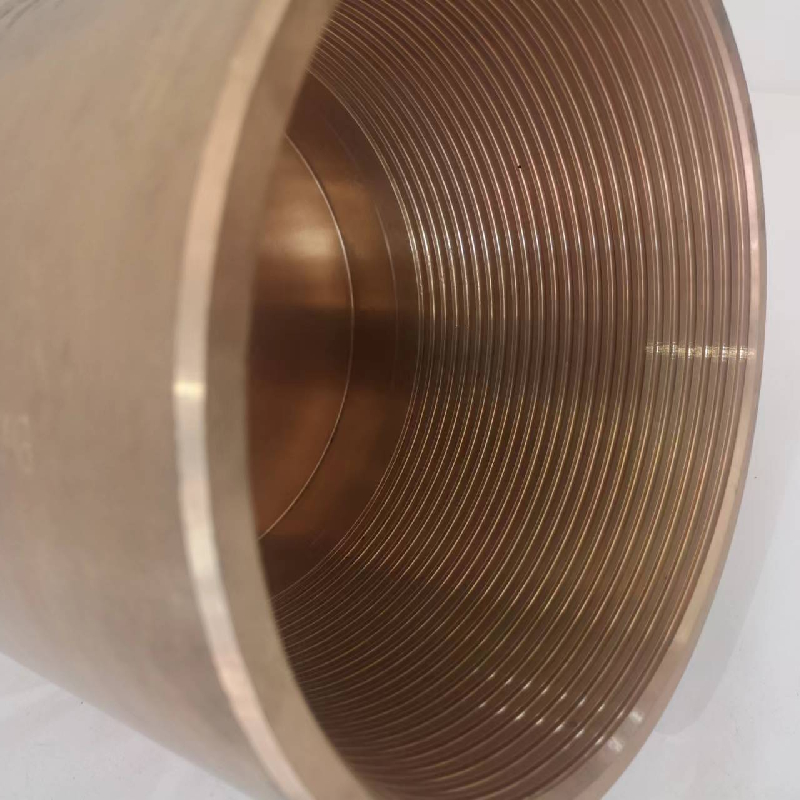
Another factor critical to the performance of seating nipples is precision engineering. The threading and profile must align perfectly with downhole tools to ensure a secure seal and reliable anchorage. Leading manufacturers employ state-of-the-art machining techniques, verified through rigorous quality assurance protocols, to achieve unparalleled accuracy and consistency. Such meticulous attention to detail not only prolongs the life of the equipment but also minimizes the risk of costly downtime due to tool failure.
Beyond material and machining, technological innovation has introduced smart seating nipples equipped with sensors. These cutting-edge devices provide real-time data on pressure, temperature, and flow rates, enabling operators to make informed decisions quickly. By integrating these sensors with advanced software, the information relay becomes seamless, facilitating predictive maintenance and optimizing well productivity. This evolution from passive to active components encapsulates the future trajectory of seating nipples.
seating nipple
When selecting a seating nipple provider, expertise and trustworthiness are non-negotiable. A reputable supplier not only provides a robust product line but also offers comprehensive customer support and service. Manufacturers with proven track records often provide field services, offering invaluable hands-on training and troubleshooting to ensure seamless deployment and operation.
It is this level of commitment that sets the industry leaders apart.
Customer feedback and case studies further reinforce trust in seating nipple solutions. Real-world applications across various geographies and reservoir types underscore their adaptability and performance reliability. Documented success stories provide compelling evidence of efficiency gains and cost reductions, thereby cementing the credibility of these products.
Moreover, compliance with industry standards, such as those set by the American Petroleum Institute (API), attests to a seating nipple's quality and safety. Adhering to these stringent benchmarks provides an assurance of quality, fostering confidence among stakeholders and reinforcing the supplier's authority in the industry.
In conclusion, the seating nipple is an indispensable tool in oil and gas operations, and its importance cannot be overstated. Through advancements in materials, engineering precision, and smart technology, these components continue to evolve, offering enhanced reliability and performance. By choosing a seating nipple from a trusted provider, operators can leverage expert design and cutting-edge technology, ensuring their wells operate at peak efficiency. As the industry continues to advance, the role of seating nipples will undoubtedly expand, solidifying their status as a cornerstone of modern well completion and management strategies.