In the realm of the oil and gas industry, the term seating nipple holds a critical place, yet it often flies under the radar compared to other components. A seating nipple is an integral piece of equipment in tubing strings, primarily serving as a catch-all anchor for subsurface control devices such as flow control devices, plugs, and gauges. Understanding the role and applications of seating nipples not only showcases expertise in the field but also enhances the operational efficiency and safety of drilling activities.
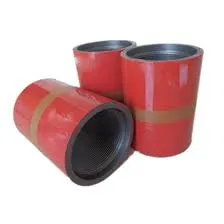
Experience gleaned from decades in the field reveals that proper utilization and maintenance of seating nipples can prevent costly delays and safety hazards. A seating nipple, typically fabricated from robust materials capable of withstanding high pressure and corrosive environments, must be precisely engineered to fit seamlessly within the wellbore surroundings. This precision engineering ensures a secure seal and alignment with other downhole equipment, facilitating smoother operations and mitigating the risk of equipment failure.
The expertise required in selecting the right seating nipple cannot be overstated. Various types of seating nipples, such as no-go nipples and selective nipples, cater to specific operational needs and well conditions. Experienced engineers often assess factors such as pressure ratings, material compatibility, and mechanical properties when choosing a seating nipple, ensuring it aligns with the intended application. For instance, in high-pressure high-temperature (HPHT) wells, material integrity takes precedence, necessitating the use of advanced alloys and testing methods to certify durability under extreme conditions.
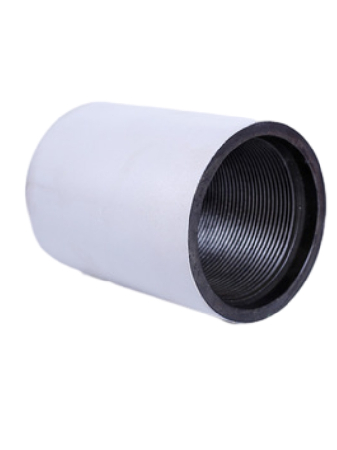
seating nipple
Authoritativeness in this domain stems from both technical knowledge and adherence to industry standards and regulations. Organizations like the American Petroleum Institute (API) provide comprehensive guidelines and standards ensuring that all components, including seating nipples, meet the requisite safety and performance benchmarks. Engineers and operators rely on these standards to maintain equipment integrity and operational efficacy, often referencing these benchmarks during procurement and inspection processes.
Trustworthiness is fostered through transparent communication and documented success stories. Case studies abound where the appropriate application of seating nipples has led to substantial operational benefits. For instance, the strategic deployment of landing nipples in a complex offshore well operation significantly reduced fluid loss and enhanced control over wellbore pressure, demonstrating the tangible advantages of their proper use. These narratives, supported by data and testimonials, reinforce the reliability and efficacy of seating nipples in critical drilling operations.
In conclusion, the seating nipple is not merely a passive component within the oil and gas apparatus but a pivotal element that demands attention and expertise.
Its role in ensuring the safety and efficiency of drilling operations underscores its importance. By drawing from extensive hands-on experience, technical acumen, and a commitment to industry standards, professionals in this field can effectively leverage the capabilities of seating nipples to drive successful outcomes. Building trust through proven performance and adherence to guidelines further solidifies the standing of seating nipples as indispensable tools in the oil and gas sector.