Stainless steel threaded couplings are quintessential components in a myriad of industrial applications, known for their robustness and unparalleled resistance to corrosion. From residential pipelines to large-scale industrial plumbing systems, these couplings have become the backbone of safe and efficient fluid transfer.
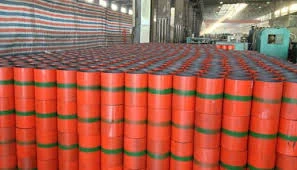
Understanding the nuances of stainless steel threaded couplings begins with acknowledging their construction. Manufactured predominantly from 304 or 316 stainless steel, these couplings offer superior resistance to rust, which is pivotal in environments with high moisture levels or those exposed to a variety of chemicals. But why stainless steel? The inherent properties of stainless steel make it not only durable but also virtually maintenance-free, a characteristic highly sought after in today’s fast-paced industrialized world.
Expertise in the utilization of these couplings is paramount to achieving optimal functionality. The threading, for instance, demands precision engineering to ensure a snug fit without the risk of leakage. Incorrect threading or improper installation can lead to significant operational inefficiencies, negating the benefits offered by the material’s superior qualities. Therefore, partnering with manufacturers who adhere to strict quality standards is non-negotiable. Choose those who can provide product integrity and confidence through compliance with ASTM or ISO guidelines.
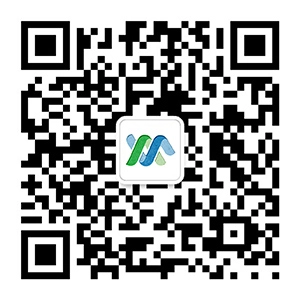
The author's authoritative knowledge of threaded coupling applications can facilitate informed purchasing decisions. For instance,
consider the varying applications of 304 versus 316 stainless steel couplings. While 304 is typically sufficient for most standard applications, coupling with 316 stainless steel becomes necessary in more corrosive environments, such as marine settings. This is due to the added molybdenum in 316, enhancing its corrosion resistance and justifying its higher cost for more demanding uses.
stainless steel threaded coupling
Practical experience underscores the importance of understanding load conditions and temperature ranges where these couplings are deployed. In environments where temperature fluctuations are extreme, stainless steel’s coefficient of thermal expansion becomes a critical consideration. It’s essential to ensure that not only compatibility with the piping material is maintained but also that the coupling exhibits resilience under these conditions, maintaining a tight and secure connection that prevents leaks or system failures.
The trustworthiness of stainless steel threaded couplings lies significantly in routine inspections and validations. Regular integrity checks ensure they function within designated pressure ratings and environmental conditions without compromise. This proactive maintenance strategy affirms their reliability, preventing potential downtimes and enhancing the lifespan of the entire system.
In conclusion, stainless steel threaded couplings are indispensable industrial components, offering unmatched durability and corrosion resistance. Successful application and longevity of these couplings hinge on a comprehensive understanding of their material properties, precise manufacturing as per standard specifications, and regular operational assessments. Users who invest time in understanding the capabilities and limitations of these components often find that not only do they prolong the life and efficiency of their systems, but they also achieve a cost-effective solution that balances upfront costs with long-term gains.
The industry’s best practices in choosing and maintaining stainless steel threaded couplings thus ensure these key mechanical joints continue to meet the evolving demands of modern engineering and infrastructure projects. Through leveraging expertise and authoritative insights, stakeholders can reliably trust their systems to operate efficiently and safely under the tenets of stringent industrial requirements.