Steel pipe couplings are essential components in the industrial sector, playing a crucial role in plumbing, heating, and cooling systems, as well as in oil and gas pipelines. These devices, which join two pieces of steel pipe, have evolved over the years to meet the demands of various applications, offering reliability and efficiency. Understanding the intricacies of steel pipe couplings can significantly impact system performance, safety, and longevity.
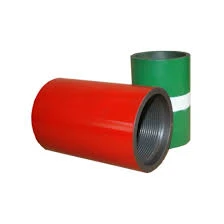
One of the most important aspects to consider when dealing with steel pipe couplings is the material selection. The couplings must withstand the same environmental conditions as the pipelines they connect, which is why durability and corrosion resistance are paramount. Stainless steel is a preferred choice due to its robustness and resistance to rust, making it ideal for use in harsh environments. However, galvanized steel is also commonly used for applications where temporary service is sufficient and cost-effectiveness is prioritized.
Precision in engineering cannot be overemphasized. When manufacturing steel pipe couplings, strict adherence to industry standards such as ASTM and ANSI is essential to ensure compatibility and functionality. These standards guarantee that the couplings can handle specified pressures and temperatures, reducing the risk of leaks and failures. Expert manufacturers meticulously test each coupling under simulated conditions, replicating the stresses and strains it might undergo in real-world scenarios.
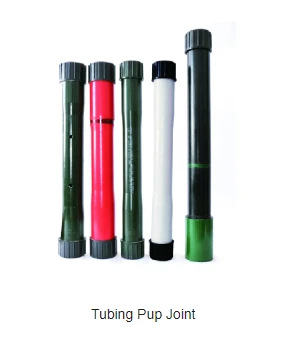
In terms of design, couplings are categorized into several types threaded, grooved, and welded are among the most common. Threaded couplings offer ease of installation, ideal for systems that may require disassembly for maintenance or upgrades. Grooved couplings provide flexibility and quick assembly, often used in large systems for their efficiency in terms of both time and labor. Welded couplings, though more permanent, ensure a robust and leak-proof connection, suitable for critical systems where reliability is non-negotiable.
steel pipe coupling
The expertise of the installation process cannot be ignored.
Even the highest quality coupling can fail if installed improperly. Therefore, selecting skilled technicians who understand the nuances of torque, alignment, and material compatibility is vital. These experts use calibrated tools to apply the precise amount of force necessary to secure connections without damaging the pipes or the coupling itself.
Authoritative voices in the industry emphasize regular maintenance checks as a core practice in preserving the functionality of steel pipe couplings. Inspections involve examining connections for signs of wear or corrosion and ensuring that coupling joints have not loosened over time due to vibrations or thermal expansion. Implementing a routine maintenance schedule extends the lifespan of the coupling system and prevents costly downtimes or catastrophic failures.
Building trust with clients in the steel pipe coupling market also hinges on transparency and the provision of warranties and certifications. Many leading manufacturers offer comprehensive warranties that cover defects or failures within a specified period, often coupled with post-installation support services. These assurances provide peace of mind to end-users, promoting a sense of reliability and trust in the durability of their installations.
In conclusion, steel pipe couplings are more than just connectors; they are pivotal to the operational integrity of many industrial systems. Their effectiveness lies in the combination of high-quality materials, precision engineering, expert installation, and ongoing maintenance. By adhering to industry standards and promoting transparency and reliability, stakeholders can maximize the benefits these components offer. Investing in superior steel pipe couplings not only elevates the performance of a system but also safeguards the long-term interests of businesses, making them a valuable asset in any industrial setup.