Threaded bull plugs are essential components in various industries, primarily within sectors dealing with fluid and gas control. As these industries demand high standards of safety, efficiency, and reliability, understanding the intricacies of threaded bull plugs becomes crucial.

Threaded bull plugs are essentially devices used to seal the end of a threaded pipe. They are quintessential in applications where the flow within a pipeline needs to be stopped temporarily or permanently. This might seem straightforward, but the role they play in ensuring operational integrity cannot be underestimated.
Selection of the right threaded bull plug is grounded in experience and expertise. Engineers and industry professionals select bull plugs based on criteria such as material compatibility, pressure ratings, temperature range, and environmental conditions. Stainless steel, Inconel, and other high-grade alloys are often chosen for their durability and resistance to corrosion, ensuring long-term reliability even in the most demanding conditions.
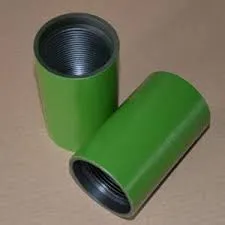
Installation is another area where experience plays a crucial role. Proper installation of a threaded bull plug involves precision and adherence to industry standards to prevent leaks or damage to the threading. Skilled technicians provide authoritative input on torque specifications and use of sealants, ensuring that each installation maintains system integrity.
Safety is a top priority when dealing with fluid and gas systems. Threaded bull plugs, while small, are critical in maintaining safety by effectively sealing the system. Industries such as petroleum, natural gas, and chemical manufacturing rely on these components to prevent the escape of potentially hazardous substances. Trustworthiness in a brand's products is often established through compliance with international standards and regular auditing, providing assurance amidst stringent industry regulations.
threaded bull plug
It's essential to understand the expertise needed in maintenance practices. Regular inspection of threaded bull plugs and their connections is necessary to assess wear and tear. Maintenance professionals emphasize replacing worn-out plugs promptly to avoid catastrophic failures, which can lead to downtime and financial losses.
Moreover, threaded bull plugs contribute to the operational efficiency of a system by ensuring that each section of a pipeline or vessel operates under optimal conditions. Efficient sealing minimizes pressure loss, which can save energy and reduce operational costs over time. Therefore, investing in high-quality, durable bull plugs is also an investment in cost-efficiency.
Choosing threaded bull plugs from reputable manufacturers is critical. Companies that possess authoritative certifications and a proven track record offer products tested under rigorous conditions. This assurance extends to customer support, providing expertise whenever technical issues arise, thus fostering a trustworthy relationship with buyers.
Advanced technology plays a role in the precision manufacturing of threaded bull plugs. Computerized numerical control (CNC) machining and stringent quality control protocols ensure that these products meet precise specifications, further enhancing their reliability and efficiency in various applications.
In conclusion, while threaded bull plugs might appear to be simple components within complex systems, their impact on safety, efficiency, and reliability is profound. Industry expertise from selection through installation, combined with a commitment to maintenance and trust in reputable brands, ensures these components function optimally often making a critical difference in industrial operations. As industries continue to evolve, so too will the technology and practices surrounding threaded bull plugs, necessitating ongoing learning and adaptation from industry professionals.