Navigating the myriad options of pipeline equipment can be daunting, especially when choosing components critical to performance and safety such as the threaded bull plug. A small yet indispensable piece of piping hardware, a threaded bull plug plays a crucial role in maintaining system integrity across various industrial applications.
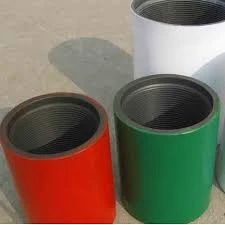
Threaded bull plugs are used to seal the end of a pipeline or to temporarily close off sections during maintenance. Constructed from high-strength materials such as carbon steel, stainless steel, or brass, the selection depends largely on the specific pressure and chemical environment it will encounter. Differentiating itself from other sealing solutions, the bull plug's threaded design ensures a secure fit that withstands high-pressure systems, coupled with the ease of dismantling when necessary.
The mastery of threaded bull plugs lies in comprehending not just the mechanical specifications, but also the operational demands of the system. For instance, in petrochemical plants where there are high concentrations of corrosive materials, stainless steel bull plugs are preferred due to their enhanced resistance to corrosion. Conversely, in water distribution networks, brass bull plugs offer an economically viable yet robust alternative.
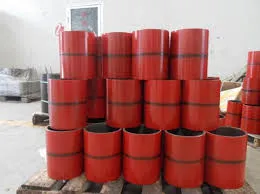
From an expertise perspective, understanding the thread design and engineering is imperative. Machinists and pipeline engineers should pay particular attention to the compatibility of NPT (National Pipe Taper) threads which are predominant in North American standards. An accurate alignment between male and female threads not only assures a leak-proof seal but also extends the lifecycle of the pipeline system by reducing wear due to vibrations and dynamic fluid pressures. Precision threading, often adhering to ASME B1.20.1 standards, ensures the interchangeability and consistent performance of these components.
threaded bull plug
In gaining experience with threaded bull plugs, practical knowledge of installation and maintenance fosters reliability in operations. Proper application of thread sealants, such as PTFE tape, can significantly enhance the seal's integrity alongside traditional metal-to-metal wedging. Regular inspection schedules for signs of thread wear or sealing degradation avoid unforeseen equipment failures and costly downtimes.
Moreover, the authority in selecting the appropriate bull plug should rest on data-backed decisions. Engaging with manufacturers or suppliers who offer certified materials and testing confirms the component's conformity to safety and engineering standards such as ANSI and API. This partnership not only provides assurance in product quality but also enables access to technical support and troubleshooting guidance.
Trustworthiness in the role that bull plugs play cannot be overstated. Many industries, including oil and gas, chemical processing, and municipal water treatment, rely on their dependable performance under extreme conditions. Proof of competency, achieved through rigorous testing and compliance with industrial certifications, establishes the credibility needed to trust these components in mission-critical applications.
In summary, threaded bull plugs might represent one of the smaller pieces in a complex industrial puzzle, but their role in ensuring safety and performance is monumental. Through a blend of expert understanding, practical experience, authoritative decision-making, and trustworthiness in material components, businesses can confidently integrate them into their pipeline systems and ensure seamless, enduring operations.