Tubing and casing play pivotal roles in the extraction and production of oil and gas. From ensuring well integrity to optimizing output, their application is essential in maintaining the lifecycle of a well. This exploration uncovers the intricacies of these components, drawing from industry expertise, practical experience, and authoritative perspectives.
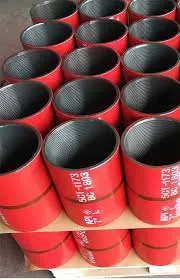
Throughout their life cycle, wells face various environmental challenges, from extreme pressures to corrosive gases. Tubing, typically smaller in diameter, serves as the primary conduit for transporting oil and gas from the bottom of the well to the surface. In contrast, casings are larger, and their primary function is to line the well, offering foundational support. They are decisive in maintaining the structural integrity of the drilled wellbore. Together, these components are indispensable in safeguarding against blowouts and maintaining the flow efficiency of hydrocarbons.
Experience in this field highlights the importance of selecting the appropriate materials and designs for tubing and casing. Different environments demand varied material strengths and coatings, such as corrosion-resistant alloys or coatings that extend their lifespan and maintain safety standards. Experience has shown that incorrect material selection can lead to early degradation, leaks, and, ultimately, financial losses. For instance, high CO2 or H2S environments require specific materials, such as chromium-based alloys, to resist corrosion effectively. The failure to implement such tailored solutions can result in significant operational failures.
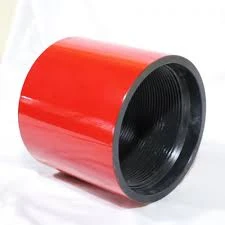
Expertise within the oil and gas industry stresses the constant evolution of tubing and casing technologies. Technological advancements such as premium connections—a crucial component—are designed to improve the sealing performance between tubing and casings, essential for maintaining pressure integrity. It is vital to understand the technical parameters such as tensile strength, collapse resistance, and burst pressure ratings to ensure that each component meets the rigorous demands of specific operational scenarios. Expertise from engineers and materials scientists often leads to the development of premium threading on tubing and casing joints, which significantly reduces the risk of leakage and enhances well safety. Understanding these subtle yet crucial differences is essential for optimized operation and safety.
tubing and casing
Authoritativeness is built on the foundation of reliance on data and global standards. Regulatory bodies often guide the specifications and standards of tubing and casing, ensuring uniformity and safety across global operations. Engineers must comply with standards set by authoritative bodies such as the American Petroleum Institute (API) to ensure well-compliance. Trust in these standards underscores the importance of adhering to them to avoid costly operational mishaps. Thorough testing and verification of these components against industry standards and guidelines further establish an operation's credibility and reliability.
Trustworthiness in tubing and casing not only revolves around product adherence to safety standards but also involves transparency in the supply chain, manufacturing process, and real-world testing. Manufacturers gain trust by providing detailed documentation and certifications for their products. Operators rely heavily on their knowledge and expect solutions that prioritize longevity, safety, and performance. A trustworthy provider will not only meet but often exceed regulatory expectations, offering warranties and field support that reflect their confidence in their products.
In conclusion, tubing and casing remain at the forefront of oil and gas operations and their advancements are crucial for the industry's future. Their evolution is supported by decades of experience, cutting-edge expertise, authoritative standards, and unwavering commitment to trustworthiness. As the industry faces new challenges with more complex reservoir conditions, the role of innovative tubing and casing solutions becomes even more critical, ensuring sustainability and efficiency for future operations. This intricate blend of performance and safety will continue to solidify the importance of these components in successful oil and gas endeavors.