Tubing collars are essential components in the oil and gas industry, playing an integral role in the extraction and transportation of hydrocarbons. Their importance cannot be overstated, and understanding their function, application, and selection criteria is vital for professionals in the field. Here, we delve deep into the world of tubing collars, highlighting their significance and providing industry insights to enhance your understanding and application.
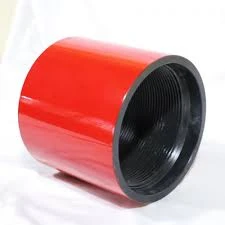
Tubing collars are threaded connectors used to join sections of tubing, which are long, hollow pipes that run from the surface into the subsurface. These collars not only hold together the tubing sections but also maintain the structural integrity of the tubing string during the well's lifecycle. This is crucial as these components must withstand extreme pressures and temperatures, making their design and material selection paramount.
The manufacturing of tubing collars involves high-grade steel or other alloys to ensure durability and corrosion resistance. The threads must be precision-engineered to prevent leaks and withstand mechanical stress. When selecting a tubing collar, engineers must consider several factors, including the environmental conditions of the well, the chemical composition of the extracted materials, and the operational pressures and temperatures.
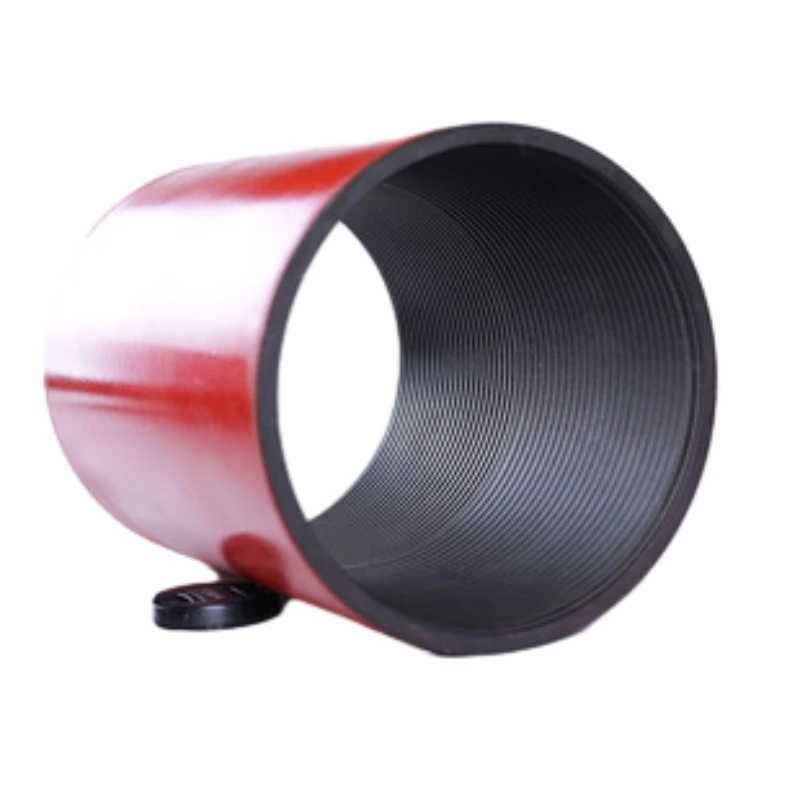
Industry expertise suggests that choosing the right tubing collar can significantly impact the efficiency and safety of drilling operations. Manufacturers conduct extensive research and development to innovate materials and designs that enhance the performance and longevity of tubing collars. Engineers rely on these insights to make informed decisions,
balancing cost, capability, and reliability.
tubing collar
Authoritative entities in the oil and gas industry provide standards and certifications that ensure tubing collars meet rigorous safety and performance criteria. The American Petroleum Institute (API), for example, offers specifications that manufacturers adhere to, guaranteeing that products can operate effectively in the challenging conditions present in oil and gas extraction.
Trustworthiness in the selection and usage of tubing collars is paramount as improper choices can lead to catastrophic failures, posing environmental and financial risks. Consequently, companies invest in quality assurance and control processes to verify that all tubing collars meet or exceed industry standards before deployment. Regular inspections and maintenance further ensure that the integrity of the tubing string is preserved over time.
Furthermore, advancements in digital monitoring and analytical tools enable operators to predict and diagnose potential issues in tubing collars before they manifest into critical problems. This predictive maintenance approach not only enhances operational reliability but also extends the life of the tubing infrastructure.
In summary, tubing collars are not mere accessories but pivotal components in the oil and gas sector. Combining experience and expertise with authoritative practices and trustworthy materials ensures that these elements perform their function reliably. The ongoing evolution in materials science and engineering continues to push the boundaries of what tubing collars can achieve, which underscores the industry's commitment to safety and efficiency. For professionals in the field, staying abreast of these developments is essential, and leveraging the latest innovations in tubing collar technology can significantly enhance operational outcomes.