Exploring the intricacies of the oil and gas industry unveils the critical role of a component often overshadowed by its more prominent counterparts—the tubing collar. In the realm of energy extraction and management, the tubing collar stands as a cornerstone of safety, efficiency, and functionality.

The tubing collar, a vital juncture in the tubing string of a wellbore, serves primarily to connect different lengths of tubing. These seemingly simple cylindrical fittings ensure the seamless transportation of oil, gas, and other materials from the earth's depths to the surface. While their function might appear straightforward, the design, material selection, and installation of tubing collars require an immense degree of expertise.
Crafted from robust materials like carbon steel and other high-strength alloys, tubing collars are engineered to withstand extreme pressures and temperatures found deep within the earth. This durability is essential, given the heavy-duty demands of the oil and gas sectors. In regions where sour gas or corrosive agents are prevalent, corrosion-resistant alloys (CRAs) are often employed. These materials, though more costly, extend the lifespan of the tubing collars and reduce long-term operational risks.
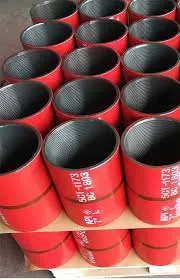
Understanding the importance of proper installation and maintenance is crucial. Experienced engineers rely on advanced technologies and precise measurements to ensure the ideal fit between the tubing and the collar, safeguarding against potential leaks and inefficiencies. Moreover, regular inspections and maintenance routines are vital in preempting failures. Non-destructive testing methods, such as ultrasonic testing and magnetic particle inspection, are frequently used to detect any signs of wear or damage without compromising the integrity of the tubing collars.
From an expertise standpoint, selecting the right type of tubing collar can significantly influence a project's success. Premium thread connections, for instance, are designed to offer superior sealing capabilities and ease of make-up, reducing the potential for operational downtime. For projects that demand high-pressure and high-temperature resistance, specifying collars with these enhanced threads can be a game-changer in maintaining operational efficacy.
tubing collar
In terms of authority, leading companies in the energy industry collaborate closely with certified manufacturers to develop custom tubing collar solutions tailored to the unique challenges of each project. Such collaborations draw on decades of combined experience and cutting-edge research to innovate and optimize tubing collar design. These partnerships underscore a commitment to adhering to industry standards and regulatory requirements, further boosting the trustworthiness of these essential components.
The trustworthiness of tubing collars is often validated through rigorous testing and certification systems. Organizations like the American Petroleum Institute (API) set stringent guidelines for the manufacturing and testing processes of tubing collars. API's specifications ensure that collars meet or exceed safety and performance standards, offering peace of mind to operators who rely on these components. A certified tubing collar manufacturer provides detailed documentation and traceability, reinforcing confidence in product quality and reliability.
Moreover, environmental considerations are increasingly influencing tubing collar innovations. As the energy industry shifts toward more sustainable practices, advanced engineering is focused on developing collars that minimize environmental impact. This includes materials that are more environmentally friendly and processes that reduce waste and emissions during production.
In conclusion, the tubing collar is more than just a connector in the chain of oil and gas extraction; it is a key player in achieving operational excellence. Expertise in selecting, installing, and maintaining these components is integral to ensuring the efficiency and safety of energy projects worldwide. The ongoing development and refinement of tubing collars, spurred by technological advancements and regulatory frameworks, continue to bolster their role as a trusted ally in the energy sector's challenging landscape.