Tubing coupling, a critical product in the oil and gas industry, acts as a connector that brings pieces of tubing together to ensure seamless flow and stability within the wellbore. The importance of tubing coupling cannot be overstated, as its design and functionality play pivotal roles in maintaining the integrity of the pipeline infrastructure. With their strategic placement along the string of pipes, tubing couplings ensure that the tubes remain tightly sealed and durable under various operational stresses.

Drawing from extensive experience in the industry, one observes that the selection of appropriate tubing coupling is vital for the smooth operation of drilling activities. It not only prevents fluid leakage, which can result in significant environmental harm and financial loss, but also maintains the pressure balance essential in deep-sea extraction. Tubing couplings are generally made from high-grade steel, which demonstrates superior resistance to corrosion, pressure, and temperature changes—factors often encountered in subterranean environments.
From a professional standpoint, it's important to emphasize the technical specifications that dictate the suitability of a tubing coupling for specific applications. The size, thread type, and material quality are critical elements that engineers consider during the procurement process. For instance, tubing couplings used in high-pressure environments require a precision engineering approach to ensure the threads are machined to exacting standards to endure the mechanical stress and thermal cycling typically experienced downhole.
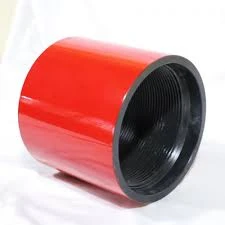
In terms of expertise, manufacturers of tubing couplings are constantly looking to innovate and improve the materials and designs used in these products. Advanced research into metallurgical properties and mechanical testing methods ensures that the products meet or exceed industry standards such as those outlined by the American Petroleum Institute (API). This rigorous emphasis on research and development is what guarantees their reliability and performance even in the most challenging environments.
tubing coupling
When discussing authoritativeness, certain established brands have made a robust mark in the industry, revered for their adherence to stringent quality control processes and ability to deliver products that meet diverse operational needs. Companies often provide detailed technical documentation and support, offering unmatched expertise to guide engineers and field workers in selecting and implementing the right tube coupling solutions.
The trustworthiness of a tubing coupling is inherently linked to both the manufacturer and the processes adopted during installation.
Missteps during the installation phase, such as improper torque application or failure to clean the coupling and tubing threads, can lead to premature failure. Therefore, partnering with vendors who provide not just top-tier products but also comprehensive training and support for installation and maintenance is crucial. This end-to-end approach ensures that the integrity of the tubing string is maintained throughout the lifecycle of the well.
Moreover, real-world case studies highlight the importance of using quality tubing couplings. For example, offshore drilling operations in areas with a history of seismic activity have shown the importance of using couplings that can accommodate ground shifts without compromising the seal of the entire tubing string. The success stories and data from these projects contribute to the ever-growing pool of operational knowledge and trust in well-designed tubing couplings.
In conclusion, the strategic significance of tubing couplings in the oil and gas industry is well established. By aligning product selection, installation, and maintenance practices with industry standards and leveraging proven expertise, organizations not only promote safety and efficiency but also bolster their reputation as reliable operators in this high-stakes field.