Tubing couplings play a pivotal role in the oil and gas industry, serving as essential components that ensure the integrity and efficiency of drilling operations. Selecting the right tubing coupling is crucial for the safety and success of the project, as a single failure can lead to disastrous results. This article delves into the unique considerations one must take into account when choosing tubing couplings, offering insights based on extensive industry experience and expertise.
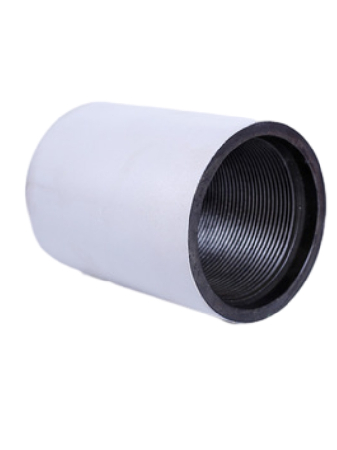
Tubing couplings are designed to connect tubing pipes securely and allow the smooth transmission of fluids without leakage. Operating in harsh and varied environments—under high pressures and temperatures—requires these couplings to be remarkably robust. Our extensive experience in the field reveals that the material composition of a tubing coupling is paramount. Steel, with its excellent strength-to-weight ratio, is the material of choice for most couplings. However, when dealing with corrosive environments, selecting couplings made from corrosion-resistant alloys such as Inconel or duplex stainless steel can prevent premature failure and extend the service life of the tubing string.
In field tests and real-world usage,
the threading on a coupling is another critical factor. Threads must be meticulously engineered to ensure a secure connection while minimizing the risk of galling—a condition where two metals stick together. API thread standards such as API 5B dictate specifications that, if adhered to, ensure compatibility and safety. Our expertise has consistently underscored the importance of using couplings that meet these rigorous standards to prevent mismatches and costly downtimes.
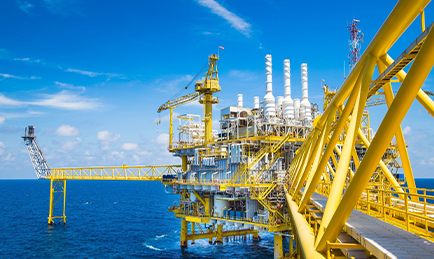
Beyond the material and threading, the coating of tubing couplings is an often underappreciated aspect that can significantly impact performance. In environments where operational challenges include exposure to hydrogen sulfide or carbon dioxide, anti-corrosive coatings are essential. Research and industry validation have endorsed the use of zinc or phosphate coatings, enhancing durability and providing a substantial barrier against corrosive agents.
Effective supply chain management plays a significant role in the procurement of tubing couplings. Trustworthy suppliers not only provide certification and traceability of materials but also maintain quality control, ensuring that every coupling meets industry benchmarks. Building a strong relationship with reputable manufacturers is vital to ensure the availability of high-quality couplings and timely delivery, thus minimizing downtime.
tubing coupling
Trust in the supplier is earned through transparent practices and consistent delivery. As seasoned industry professionals attest, working with an ISO-certified manufacturer ensures the highest standard of quality assurance. Whether the need arises for custom sizes or specific threading configurations, collaborating with a responsive and adaptable supplier can make all the difference in a project's success.
Moreover, technological advancements have seen the integration of automated inspection processes in the manufacturing of tubing couplings. Utilizing ultrasonic and magnetic particle inspection techniques detects any potential flaw well before deployment. As documented by industry leaders, adopting these modern inspection technologies is not only cost-effective but also crucial in upholding operational safety.
Finally, innovations in digital analytics provide a new horizon for enhancing E&P operations. Data collected from sensors embedded within tubing couplings can predict potential failures and optimize maintenance schedules. This data-driven approach offers a predictive maintenance model, reducing unforeseen interruptions and budget overruns.
In conclusion, tubing couplings are more than just an accessory in the oil and gas sectors; they are fundamental to the safe and effective transport of valuable resources. Selecting the right coupling involves a balance of materials, threading, coatings, supplier reliability, and modern technology. By appreciating these multifaceted elements, decision-makers ensure both the robustness and longevity of their tubing operations. This comprehensive approach not only aligns with industry best practices but also establishes a standard of excellence in drilling operations worldwide.