In the ever-evolving world of the oil and gas industry, tubing couplings play an indispensable role, ensuring seamless operations throughout various processes. A tubing coupling is a short length of pipe used to connect two pieces of tubing or to close the ends of a pipeline. Its application, though seemingly straightforward, requires a deep understanding of its variations, materials, and installation processes to ensure efficiency and safety in the field.
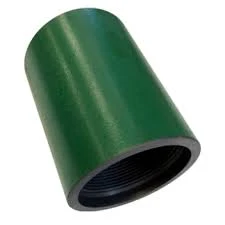
Tubing couplings are designed to withstand the extreme pressures and temperatures that are inherent in oil and gas extraction environments. Selecting the right tubing coupling requires an understanding of several essential aspects.
One must appreciate the material from which the coupling is made. Typically, they are manufactured from high-grade steel to endure the wear and tear imposed by harsh operational environments. Stainless steel and alloy steel are common choices due to their corrosion resistance and strength. An optimal coupling is characterized by its ability to withstand not only physical stress but also chemical exposures, such as those from hydrocarbons.
Expertise in selecting tubing couplings arises from extensive field experience and technical knowledge. It's critical to consider the specifications outlined by the American Petroleum Institute (API), which sets the standards for the design and manufacturing of couplings. API 5CT standards, in particular, are globally recognized and adhered to in ensuring the quality and compatibility of tubing couplings with other pipe elements. Adhering to these standards not only guarantees the integrity of the coupling but also affirms its reliability in preventing leakages that could lead to environmental hazards and operational disruptions.
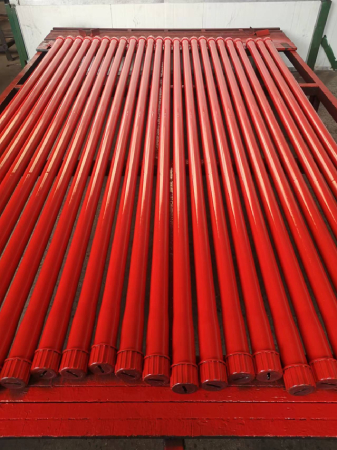
Furthermore, the choice of the correct coupling is heavily influenced by the type of well operation, whether it's for a drilling rig or production tubing. Each application demands a specific configuration to minimize downtime and maximize productivity. Wearing the hat of an expert involves assessing the coupling thread forms—round, buttress, or premium connections—to ensure they fit precisely and maintain a seal under pressure variations that are typical in oil and gas extraction.
Beyond material and configuration, attention must be given to the presence of any coating applied to the couplings. Coatings serve to enhance the lifespan of the coupling by protecting against rust and scale, which could compromise the structural integrity over time. In environments with high salinity or acidity, specialty coatings might be imperative for ensuring longevity and operational consistency.
tubing coupling
The longevity and effectiveness of a tubing coupling also depend heavily on the installation process. Proper installation requires trained personnel who understand the nuances of torque application, the importance of correct alignment, and the significance of properly securing the couplings. This ensures a tight seal, preventing the passage of fluids between the tubing and the couplings which could otherwise cause significant pressure loss and potential environmental risks.
Trustworthiness in any tubing coupling manufacturer is built over years of demonstrated reliability, adherence to quality standards, and continuous innovation in product design. Manufacturers who invest in research and development tend to offer products that meet or exceed industry standards, often providing tailored solutions for specific operational needs. Such a dedicated approach positions manufacturers as authoritative sources within the oil and gas sector, fostering trust among their clientele.
Transcending the data sheets and technical jargon, real-world experience shared by industry veterans provides invaluable insights into selecting, maintaining, and replacing tubing couplings. Lessons learned from the field often highlight potential pitfalls and underscore the importance of routine inspections and maintenance schedules to detect early signs of wear or corrosion.
In sum, mastery over the selection and application of tubing couplings requires a blend of technical knowledge, compliance with industry standards, thoughtful installation practices, and a commitment to product maintenance. The ever-demanding environments of oil and gas extraction necessitate that each coupling not only performs reliably but does so with the confidence of industry-proven practices behind it. For operators, leveraging the expertise and trust established by authoritative manufacturers ensures that their operations remain smooth, efficient, and safe.