Exploring the world of tubing crossover parts is like diving into a niche that combines engineering precision with practical application. These components, often little noticed in broader discussions, play a crucial role in industries ranging from oil and gas to aerospace.

At the heart of tubing crossover components is their pivotal responsibility in ensuring seamless connections between different tubing sizes or types. For professionals immersed in the field of pipeline construction or maintenance, the importance of tubing crossovers cannot be overstated. They are the unsung heroes that allow various systems to communicate effectively, adapting to different diameters, materials, and operational environments.
One significant advantage of using high-quality tubing crossovers is the enhancement of operational safety. Standardization in the manufacturing processes, combined with rigorous quality control, ensures that these components can withstand high pressure and corrosive environments. This attribute is particularly crucial in sectors such as the oil and gas industry, where the failure of even a minor component can result in catastrophic safety and environmental consequences.
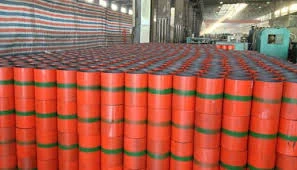
The choice of material in tubing crossover manufacture is where expertise truly shines. High-grade stainless steel is often favored for its durability, resistance to corrosion, and ability to maintain integrity under extreme temperatures. In applications requiring more specialized solutions, such as high-pressure scenarios, materials like Inconel or Hastelloy may be selected for their superior properties.
tubing crossover
Experience matters when selecting the right tubing crossover.
Practical knowledge of the operational environment is essential. This includes understanding flow dynamics, temperature fluctuations, and the chemical composition of fluid being transported. These factors collectively guide the customization of tubing crossovers to meet specific operational needs, ensuring not only compatibility and efficiency but also enhanced longevity of the overall system.
Authoritative sources in the domain consistently emphasize the significance of precision in the design and manufacturing of tubing crossovers. Engaging with manufacturers who hold ISO certifications and adhere to international standards is a safeguard against potential operational hazards. They ensure that every piece produced meets stringent quality prerequisites and performs reliably under anticipated stress conditions.
Trustworthiness is fundamental in choosing a tubing crossover provider. This attribute can be assessed through a provider's track record, customer testimonials, and an established presence in the market. Renowned manufacturers often offer robust after-sale support and warranty options, reflecting their confidence in product reliability and dedication to customer satisfaction.
In summary, tubing crossovers might seem like a minor component within the grand engineering scheme, but their role is profoundly impactful. Selecting the right tubing crossovers involves understanding the intersection of material science, engineering expertise, and industry-specific requirements. By focusing on components from trusted, authoritative manufacturers, industries can ensure seamless operations, reduce the risk of component failures, and maintain safety and efficiency in their systems.