Tubing crossover is a pivotal component for anyone in the oil and gas industry, and mastering its complexities can significantly enhance both operational efficiency and productivity. This small yet incredibly significant element of drilling operations serves as a bridge between different sections of tubing, ensuring a seamless transition and preserving the integrity of the flow path. However, the intricacies involved in choosing, installing, and maintaining tubing crossovers require a deep understanding, combining experience, expertise, authoritativeness, and trustworthiness.
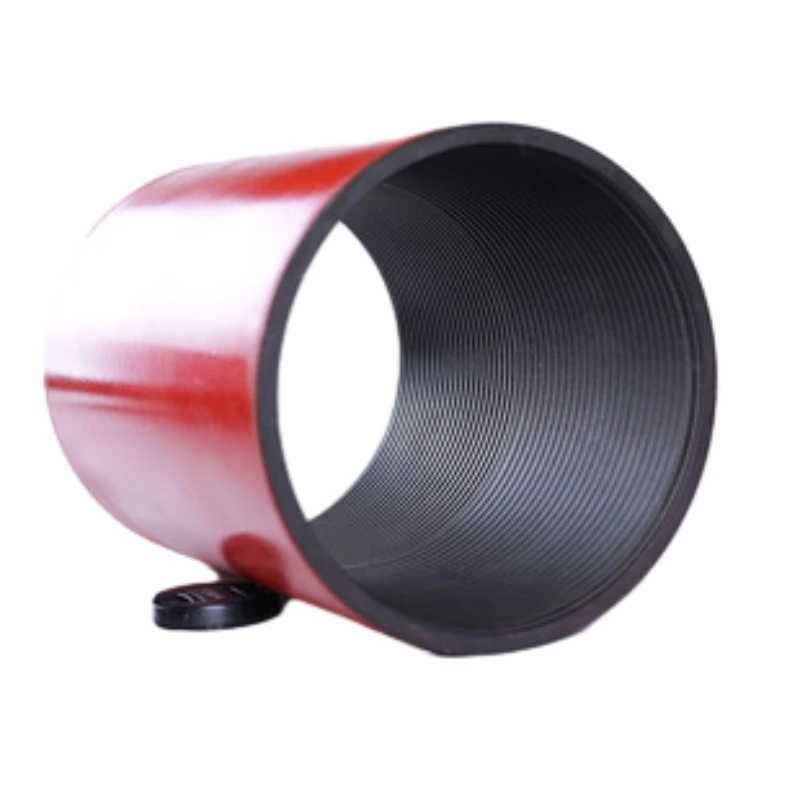
When it comes to tubing crossovers, understanding the types and their specific applications is crucial. Typically,
they're employed to connect tubing strings of different diameters or thread types. Each crossover varies in design to suit different applications, which could include transitioning from one tubing size to another, adapting to a different thread type, or facilitating a change in material specifications to withstand varying pressure and environmental conditions.
The experience of manufacturers and operators plays a significant role in the lifecycle and performance of a tubing crossover. Seasoned professionals will attest to the importance of selecting a crossover that matches not only the physical pipeline requirements but also the operational conditions. For instance, choosing the correct grade of metal based on whether the operation is onshore or offshore, and accounting for potential corrosion, temperature extremes, and pressure variances, all contribute to ensuring longevity and reliability.
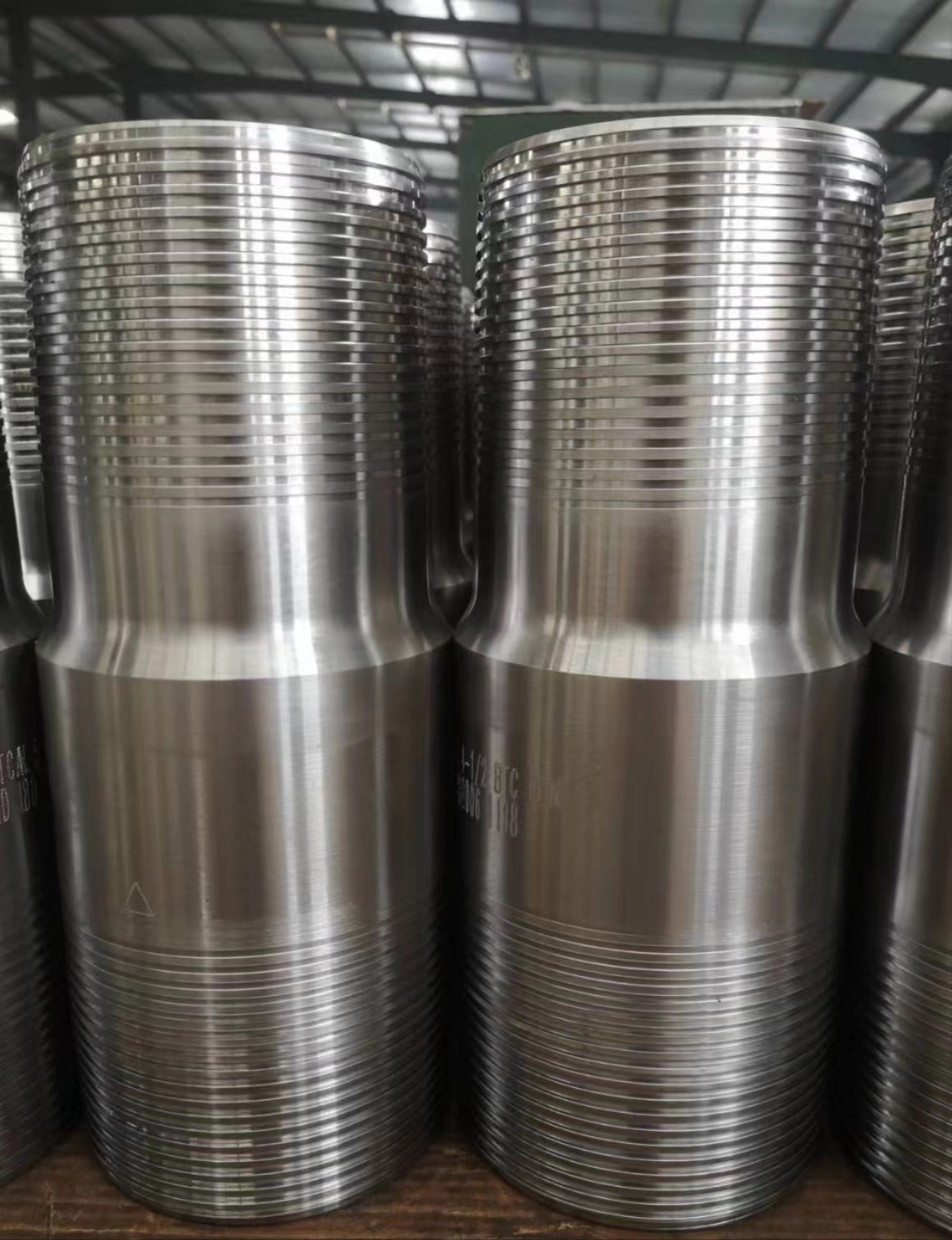
Expertise in the field of tubing crossovers demands a thorough understanding of metallurgy, precision engineering, and the specific demands of the oil and gas sectors. Technical specifications such as yield strength, tensile strength, and hardness should align with the intended use. An expert's insight into how these elements interact with various fluids and gasses can prevent premature failure, avoiding costly downtime.
tubing crossover
Authoritativeness in this niche is often demonstrated by those who have designed or worked extensively with these essential components. Engineers and seasoned field operators provide invaluable knowledge through published papers, case studies, and conference presentations. Their insights often lead to innovations in crossover design and manufacturing, adapting to new challenges posed by deeper and more complex well environments. Being aware of and incorporating these authoritative sources into your operation can lend significant advantages.
The trustworthiness of a tubing crossover is determined by the consistency with which it maintains its integrity under specified conditions. This reliability stems from rigorous testing and quality assurance by manufacturers. To select a trustworthy crossover, operators should look for certifications that ensure compliance with industry standards, such as API (American Petroleum Institute) specifications. The reputation of the manufacturer and their adherence to these standards further enhance trust in the product. Moreover, customer testimonials and field data are invaluable resources that reflect real-world performance, ensuring that decisions are based not only on theoretical data but also on practical outcomes.
In terms of product availability and technological advancements, the tubing crossover market continues to evolve. With the rise of digital monitoring and smart technology integration in pipelines, some crossovers now come equipped with sensors to monitor pressure changes and temperature, providing real-time data to operators. This layer of innovation helps in predicting failures before they occur, thereby significantly improving operational efficiency.
To summarize, selecting the right tubing crossover involves a balance of experience, expertise, authoritativeness, and trustworthiness. Proper match with the operational environment, adherence to engineering and metallurgical standards, and gaining insights from authoritative industry figures lead to informed decision-making. Ultimately, ensuring reliability through rigorous testing and leveraging new technological advancements can set operations on a path to enhanced performance and longevity. In the rapidly progressing oil and gas sector, keeping abreast of these nuances can make the difference between operational success and costly oversights.