Tubing crossovers represent a pivotal element in the oil and gas industries, serving as a critical component in well integrity management. These precision-engineered connectors are indispensable in facilitating the transition between tubing strings of varying sizes, thus ensuring seamless fluid transport and maintaining optimal system efficiency.
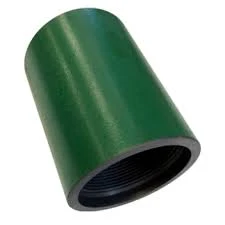
Crossovers are typically manufactured using high-strength steel or other robust alloys, which ensures longevity and reliability under intense pressure and corrosive environments. Selecting the right material is essential; it must withstand the physical and chemical demands of downhole operations. As an experienced industry professional with a comprehensive understanding of tubing crossovers, I can attest to the fact that superior material choice not only extends the lifecycle of the crossover but also contributes to the overall safety and performance of the well.
One of the primary considerations when selecting a tubing crossover is compatibility with the production tubing. The crossover must provide a tight seal to prevent fluid leakage, which is crucial for maintaining well integrity and preventing costly downtime. Engineers often emphasize the importance of precise measurements and high-quality manufacturing standards, as these factors significantly influence crossover efficiency and reliability. Through my work, I have seen firsthand how investing in high-quality crossovers can lead to reduced maintenance needs and enhanced operational performance.

Another critical aspect of tubing crossovers is their design, which demands expert knowledge and engineering prowess. The design process must account for the specific environmental conditions and pressure differentials encountered in each application. Engineers must evaluate the crossover’s capacity to handle these conditions without compromising the structural integrity of the entire tubing system. Techniques such as finite element analysis are commonly employed to simulate stress and predict potential failure points, ensuring that the crossover can withstand the harshest operational scenarios.
tubing crossover
In operation, tubing crossovers play a vital role in mitigating risk and enhancing productivity.
They enable operators to adapt their tubing strings to accommodate changes in production rates and reservoir conditions. Flexibility in tubing size transition is vital; it allows for scalability in operations, ensuring that the tubing system can evolve alongside the field's needs. Over the years, I have found that successful operations stem from a well-designed crossover strategy, which provides the adaptability required in dynamic settings such as offshore drilling or high-pressure, high-temperature (HPHT) environments.
From a maintenance perspective, the choice and application of crossovers must also consider ease of installation and inspection. It is crucial that these components are designed with consideration for the frequency and simplicity of maintenance operations. Features such as snap-in installations or modular designs can greatly reduce the time and effort needed to service these parts, which is an aspect often celebrated by technicians in the field. In my experience, solutions that streamline maintenance directly contribute to operational efficiency and reduce the long-term costs associated with tubing interventions.
Furthermore, another emerging area of innovation in tubing crossovers is the integration of sensor technology. Smart crossovers equipped with sensors and real-time data transmission capabilities offer unprecedented insight into the downhole environment. These technologies not only provide critical performance data but also enable predictive maintenance, anticipating potential failures before they occur. The industry is moving towards data-driven decision-making, and incorporating smart technology into crossovers is a step toward more efficient and proactive well management.
Conclusively, the successful implementation of tubing crossovers demands a blend of empirical experience and cutting-edge expertise. As materials science advances and technology evolves, the design and functionality of tubing crossovers continue to improve, providing operators with reliable and efficient solutions for challenging extraction environments. For anyone engaged in the oil and gas sector, understanding the complexities and technological advancements associated with tubing crossovers is not merely advantageous but indispensable.