The well casing coupler is an indispensable component in the construction and maintenance of modern oil and gas wells. Ensuring the integrity and functionality of these couplers is vital to successful drilling operations. Combining both practical experience and expert insights, this article delves into why well casing couplers are critical, how they work, and what factors make a choice of coupler reliable and effective.

In the ever-evolving field of oil and gas extraction, the need for durable and efficient equipment cannot be overstated. Well casing couplers serve as the integral connectors between different sections of casing pipes, which are used to line the wellbore. Their primary function is to ensure a secure and leak-proof connection that can withstand the immense pressures and environmental challenges encountered during drilling operations.
Well casing couplers are engineered with precision to handle the adverse conditions deep beneath the earth's surface. This includes exposure to high pressures, corrosive substances, and temperature fluctuations that can jeopardize the structural integrity of less robust components. A coupler's ability to maintain its performance and reliability under these conditions speaks to its engineering and design excellence.
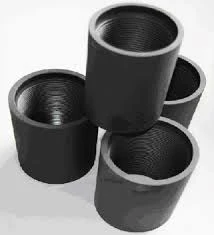
For oil and gas companies, the repercussions of choosing an inadequate well casing coupler can be severe. Any failure can lead to expensive delays, environmental damage, and safety risks. Hence, the criteria for selecting these couplers extend beyond basic material properties, encompassing advanced features such as thread design compatibility, seal integrity, and ease of installation. A well-designed coupler minimizes downtime and ensures smooth operational continuity, which can translate into significant cost savings.
well casing coupler
Drawing from decades of field experience, drilling experts emphasize the importance of choosing well casing couplers from manufacturers with proven track records. Such companies often provide detailed documentation and testing reports that demonstrate compliance with industry standards and regulations. Moreover, expert-reviewed certifications and endorsements act as additional layers of assurance regarding a product’s quality and performance.
On the engineering side, well casing couplers are subjected to rigorous testing processes, including tensile and compression tests, to simulate field conditions. It is imperative for engineers to analyze test data to predict the longevity and failure rates of these components. Advanced finite element analysis (FEA) is often employed to understand stress distribution patterns and potential failure points under various load conditions.
Trust forms the backbone of any relationship between suppliers and buyers of well casing components. Thus, establishing a reliable supply chain for high-quality couplers becomes essential. Companies often integrate quality assurance programs to ensure each batch of couplers meets stringent quality benchmarks. This involves dimensional inspections, pressure testing, and corrosion resistance assessments, which together certify the couplers' readiness for deployment in extreme environments.
In summation, the efficacy of well casing couplers hinges on both their engineering brilliance and the overall commitment to quality by their manufacturers. A thorough understanding of the design principles, coupled with expert insights into material science and mechanical properties, equips stakeholders to make informed decisions. By doing so, they manage to not only boost the efficiency of drilling operations but also mitigate potential hazardous impacts, ultimately reinforcing the trust in modern energy extraction methodologies.