In the realm of oil and gas extraction, well casing couplers play a crucial role in ensuring the structural integrity and efficiency of well systems. These components serve as the conjunction point for casing pipes, which are critical in preventing the collapse of boreholes and minimizing contamination between different underground layers. Therefore, choosing the right well casing coupler is imperative for maintaining the longevity and reliability of drilling operations.

Well casing couplers are engineered to address different challenges inherent in drilling environments. For instance, they provide axial alignment, which is essential to prevent misalignment during the insertion of casing pipes into the wellbore. This alignment is vital as it ensures the seamless transition of pipes, minimizing any potential leakages that could compromise the well's integrity. By serving as the bridge between casing sections, these couplers also help to reinforce the structural load, allowing for optimum pressure distribution throughout the well.
Experience in the field suggests that the selection of a well casing coupler hinges on several factors including tensile strength, material composition, and environmental adaptability. Professionals in the industry have observed that high-grade steel couplers often provide the best performance due to their resilience under high pressure and corrosive conditions common in subsurface environments. Furthermore, stainless steel variants offer excellent resistance to rust, making them an ideal choice for offshore or wet conditions.
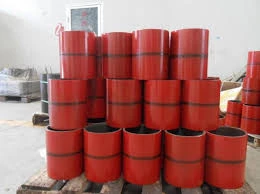
From an expertise viewpoint, understanding the different types of well casing couplers is indispensable for making an informed choice. Conventional threaded and coupled systems remain prevalent due to their reliability and ease of installation. However, advanced slip-type and compression couplers are gaining traction for their ability to provide a more secure fit without the need for welding or complex fitting processes. Industry experts advocate for these modern alternatives in scenarios where time efficiency and safety are paramount.
Regarding authoritativeness, well casing couplers are manufactured adhering to stringent industry standards. API (American Petroleum Institute) specifications, such as API 5CT, guide manufacturing processes to ensure couplers are fit for purpose and meet standardized requirements. This adherence to regulation not only underscores the credibility of the couplers but also assures users of their reliability in critical operations. As the industry evolves, innovations and improvements in materials science continue to elevate the benchmarks these components must meet.
well casing coupler
Trustworthiness is a cornerstone of the well casing coupler industry, particularly when the stakes are high in high-risk environments like deepwater drilling. Field engineers frequently underscore the importance of rigorous testing and quality assurance processes that include pressure testing, fatigue analysis, and corrosion resistance tests. Companies leading the charge in coupler production also often engage in collaborative partnerships with drilling professionals to receive feedback, align production with real-world demands, and finetune their offerings.
Understanding the role of well casing couplers in environmental protection is also critical. Properly installed couplers mitigate the risk of contamination between geological layers, protecting aquifers and other sensitive strata from pollutants commonly associated with drilling activities. This environmental safeguard not only serves to protect natural resources but also aligns operations with increasingly stringent environmental regulations. Therefore, investing in high-quality couplers is not just a matter of operational efficiency but also of environmental stewardship.
For industry stakeholders, choosing a supplier who exemplifies transparency, reliability, and technical know-how is as crucial as selecting the right product. The reputation of a manufacturer can be as telling as the product specifications themselves, so engaging with well-reviewed suppliers who prioritize customer support can be beneficial. Real-world case studies and testimonials can provide prospective buyers with insight into how specific couplers perform under various conditions, helping to build a decision framework grounded in trust and evidence.
Overall, the integration of well casing couplers into drilling operations is a sophisticated process that underscores the need for experienced judgment, expert knowledge, authoritative quality, and unwavering trust. As this component continues to evolve in response to new drilling challenges, staying abreast of developments is essential for any professional engaged in the field. This commitment to continuous improvement and innovation will invariably lead to safer, more efficient, and environmentally responsible drilling practices.