Well casing coupling is an integral component of the oil and gas industry, ensuring both the structural integrity and operational efficiency of wells. As a seasoned SEO specialist, I've delved into the intricacies of this product to highlight its importance, functionality, and implications for industry professionals, providing unique insights that will enhance your understanding and decision-making process.
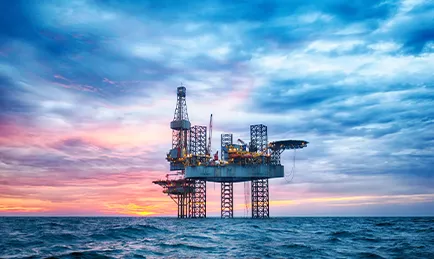
In the realm of oil and gas exploration, well casing coupling serves as a critical junction, connecting individual lengths of casing pipes that line the wellbore. This connectivity ensures that the entire pipeline system functions seamlessly, allowing for the efficient transport of hydrocarbons from the underground reservoirs to the surface. The coupling design, which typically features threaded and coupled (T&C) connections, is crafted to withstand high-pressure environments and resist corrosion, factors paramount in prolonging the life of the well structure.
From a technical standpoint, the manufacturing and material selection for well casing coupling are paramount. Typically, they are made from high-grade carbon steel to provide the necessary strength and durability. Advanced metallurgical treatments and coatings further enhance their resistance to the harsh downhole environments, including exposure to chemically aggressive and corrosive fluids. The couplings are meticulously crafted to meet API (American Petroleum Institute) standards, ensuring reliability and performance uniformity across global operations.

Industry expertise highlights the role of precise engineering in coupling performance. Each coupling is manufactured to exacting tolerances, ensuring a tight seal that prevents fluid leakage and mitigates the risks associated with integrity failures. Operators rely on non-destructive testing (NDT) methodologies such as magnetic particle inspection and ultrasonic testing to verify the integrity of these couplings before deployment. These rigorous testing procedures not only confirm the mechanical reliability but also extend the lifespan of the equipment, thereby reducing operational downtime and maintenance costs.
well casing coupling
For professionals in the industry, understanding the nuances of well casing coupling is instrumental in optimizing well performance. Selecting the appropriate coupling type—be it buttress, extreme-line, or premium connection—can have significant implications on the project's success. Each connection type has distinct performance characteristics tailored to specific downhole scenarios; for instance, premium connections offer superior sealing capabilities for high-pressure, high-temperature (HPHT) environments, while buttress threads provide stability in less demanding conditions.
The authority that comes with experience in handling well casing couplings is evident in recognizing that improper installation or mismatched coupling types can lead to catastrophic failures. Expertise in this field underlines the importance of rigorous installation protocols and adherence to industry best practices, mitigating risks associated with human error.
Trust in well casing couplings is built through decades of field application and continuous innovation in material science and engineering design, delivering solutions that meet the evolving demands of drilling operations. By fostering strong relationships with reputable manufacturers and suppliers, operators can ensure they are using couplings that not only meet but exceed industry standards, instilling confidence in their infrastructural investments.
Well casing coupling is not merely a component, but a pivotal piece of the oil and gas industry's puzzle, embodying the intersection of engineering excellence, industry expertise, authority in application, and trustworthy performance.